Innovative manufacturing processes for climate-neutral aircraft
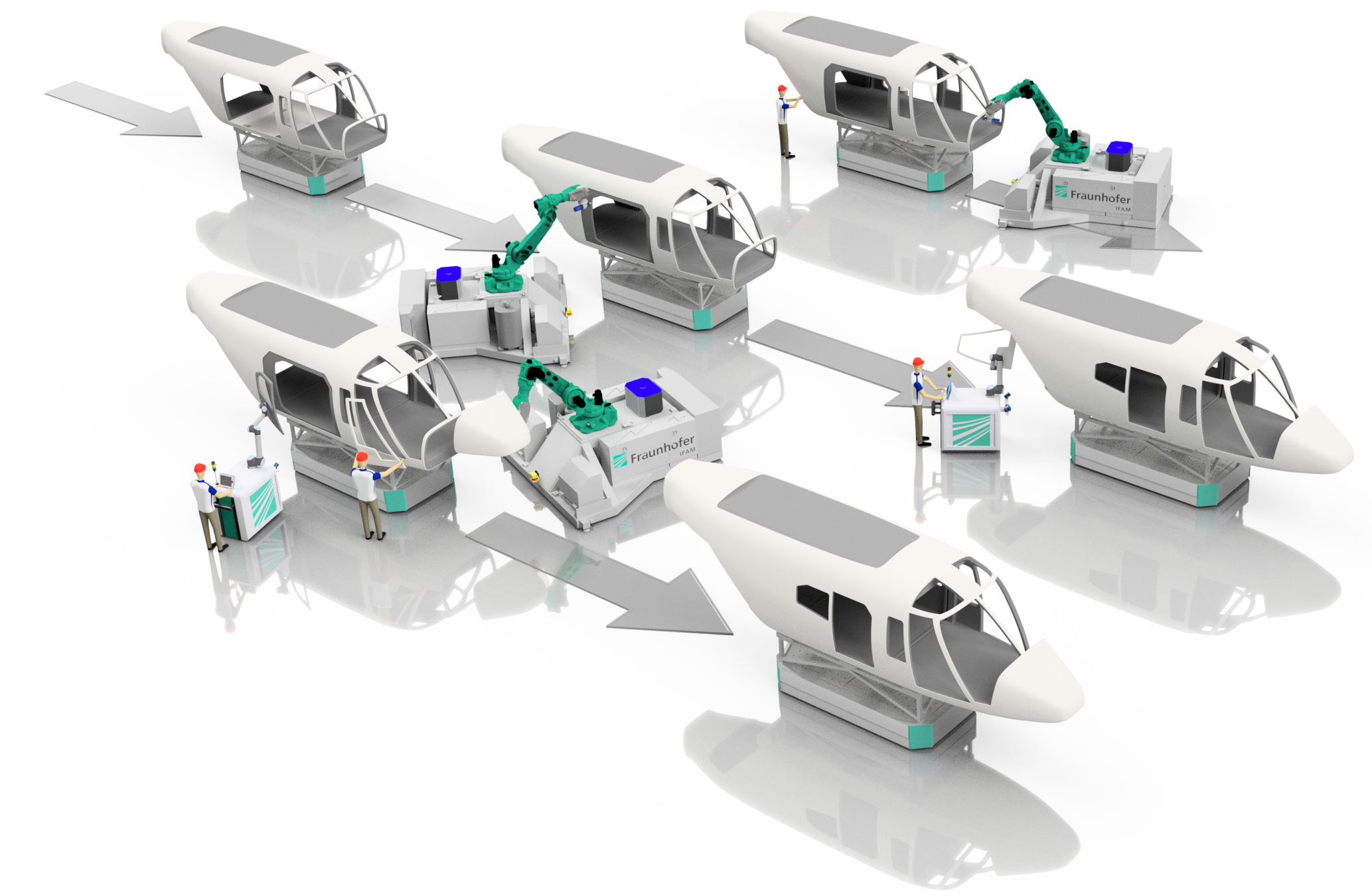
Aviation in Europe must be climate neutral and sustainable along the entire value chain by 2050. To achieve this, climate neutral aircraft must be available from 2035. New materials and manufacturing processes are also a key prerequisite for this.
With the aim of creating a sustainable aviation industry of tomorrow, Fraunhofer IFAM is collaborating with partners to conduct research in a variety of areas ranging from material and manufacturing technology to application for climate friendly aircraft. Research activities in this field include, for example, resource efficient painting processes, mobile holding fixtures for large aircraft structures, and new assembly approaches for helicopters.
Painting processes for aircraft structures are a central component of the production chain. They also play a role in the further life cycle of the aircraft, as the paint is regularly renewed at certain maintenance intervals and as part of repairs. In context of the BELLISSIMA research project funded by the BMWK, both process times and paint quantities are to be reduced by means of demand-oriented digitized laser paint stripping, automated pretreatment processes and edge-sharp painting processes.
Non-productive times in aircraft manufacturing and assembly are significant due to handling and alignment processes in production lines. They thus unnecessarily extend throughput times and make the production chain more inefficient, also from an ecological point of view. As part of the UniFix joint project funded by the BMWK, Fraunhofer IFAM and its cooperation partners have developed a mobile holding fixture which flexibly picks up aircraft structural components, aligns them precisely in terms of shape and transports them automatically between the work stations. This significantly increases productivity, efficiency, and cost-effectiveness.
Tolerance-compensating measures in the context of structure assembly, so-called shim processes, which are currently primarily carried out manually, also have a negative influence on the efficiency of assembly systems. Approaches to improve this are currently being investigated in the joint COBAIN project, which is funded by the BMWK and uses helicopter structures as an example. The central approach is a metrological measurement of the component geometry, which is used as input for a virtual assembly to determine the individual gap between the joining partners. This enables a precisely fitting shim process that compensates for the geometric individuality of the joining partners and enables assembly in a single step.