Center for Networked Surface and Coating Technology researches the use of industrial robots and virtual/augmented reality in surface treatment
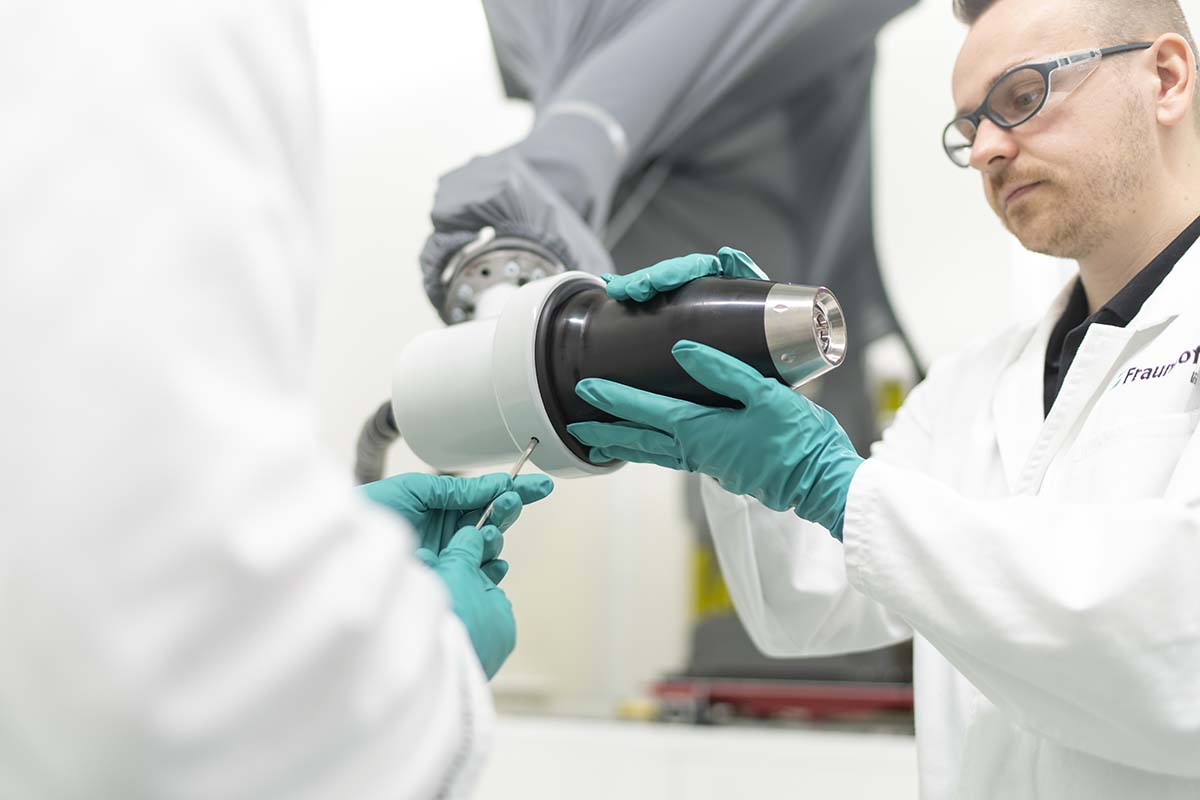
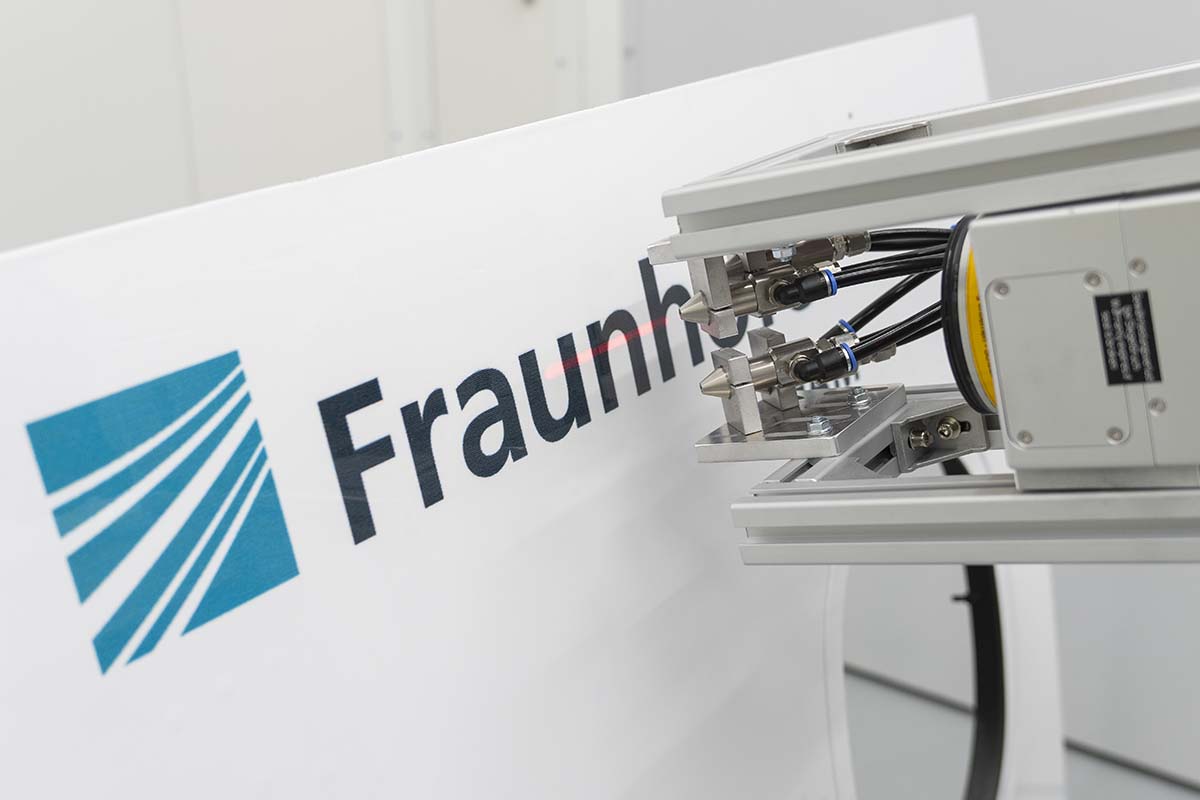
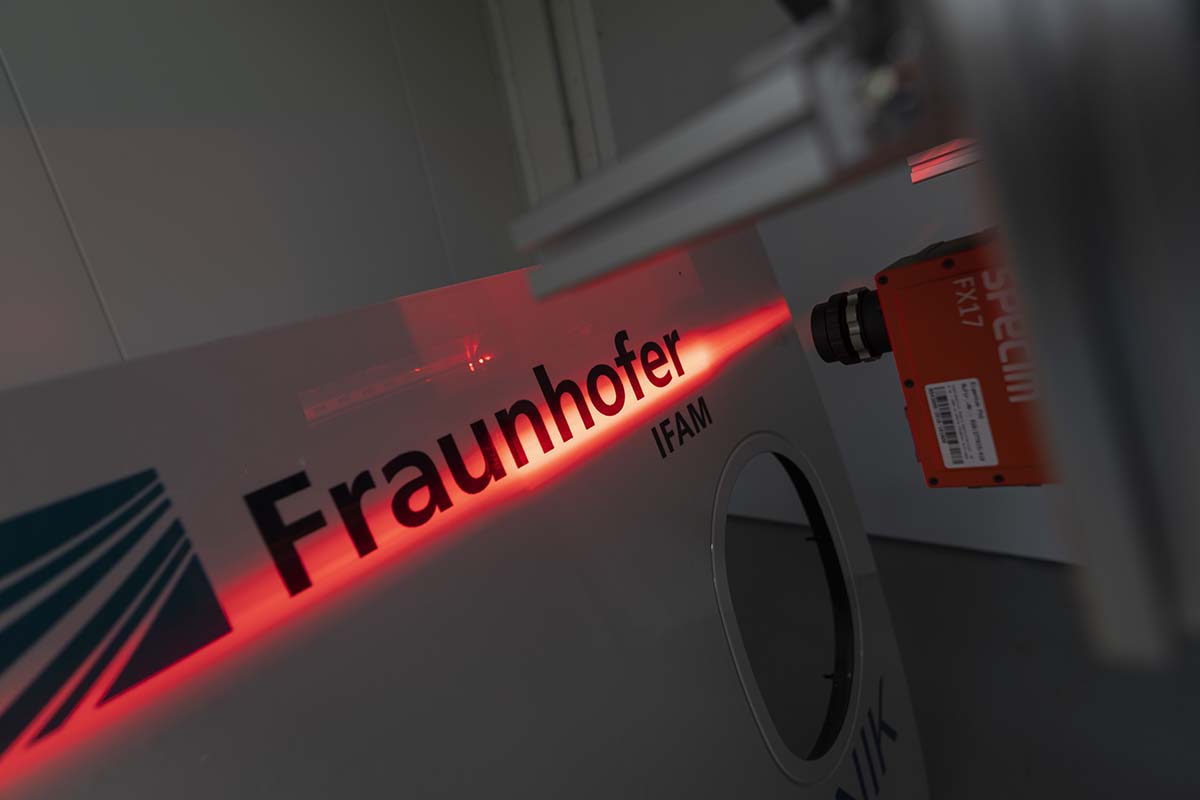
The "Center for Surface and Coating Technology" at Fraunhofer IFAM demonstrates the future of surface treatment. The state-of-the-art technical center has digitally linked industrial robots – such as painting robots – for the automated cleaning, pre-treatment, and subsequent painting of component surfaces in small and large structures. The entire process chain is digitally mapped and supplemented by interaction options using virtual and augmented reality. R&D goals include the realization of digitally networked surface technology systems and processes as well as process and quality optimization through machine learning and the use of AR/VR methods.
Industry 4.0 is no longer a buzzword
Fully automated and digital processes are nowadays a must in the industrial treatment and processing of component surfaces – especially with regard to flexibility, process efficiency and quality assurance. Costs are reduced, quality improved, throughput rates increased and material savings realized. Last but not least, the occupational safety of employees is also improved.
The current challenge is the complete digital networking of all work steps including the technology used in surface treatment and coating processes. Furthermore, the possibilities of automation and digitization are far from exhausted when it comes to control and quality assurance along the entire process.
When virtual reality becomes reality in industrial practice
Virtual reality, augmented reality, Internet-of-Things applications – digital tools and methods that link virtual models with real components are also increasingly finding their way into surface treatment and coating processes. If implemented correctly, they offer enormous potential for product development, process efficiency and quality assurance. Challenges that companies need to get to grips with here include:
- Storing and managing relevant data
- creation of reliable models and robust simulations
- correct data provision and continuous data flow along the entire process chain
- automated inclusion of relevant data to optimize process steps
- integration of interfaces for human-machine interactions
Industry representatives immediately recognize the benefits of such digital tools and methods, but integrating them into their own treatment and painting processes is extremely complex.
Center for Networked Surface Coating Technology
Fraunhofer IFAM has set up the Center for Networked Surface and Coating Technology precisely to research such current issues. The center offers project partners an automated paint booth and robotic cells for pretreatment, quality assurance, and painting of small and large structures. In addition to the actual pretreatment, painting, and quality assurance processes, evaluation and visualization of the process and measurement data is performed using AR/VR and edge computing. The center combines the expertise from the departments "Paint and Lacquer Technology", "Plasma Technology and Surfaces", and "Quality Assurance and Cyber-Physical Systems" of Fraunhofer IFAM.
In the future, Fraunhofer IFAM experts will develop and test new processes for surface treatment and coating here. On the one hand, the center is used for application-oriented and practical research and development work. On the other hand, commercial coating processes can be simulated and optimized.
Adaptable, modular technologies for pretreatment and cleaning
For cleaning and activation of component surfaces for reliable adhesion, various pretreatment processes can be adapted in the Center for Networked Surface and Coating Technology. For critical contamination, abrasive technologies such as vacuum suction blasting, CO2 snow blasting or brush cleaning can be used. Abrasive laser processes in the IR and UV range completely remove release agents but also local contamination such as bird droppings. In addition, atmospheric pressure plasmas, VUV lamps - or moderate laser processes can be used for fine cleaning and functionalization of surfaces. Due to the adaptability of all processes, combined processes can also be carried out as required for repair processes including local decoating.
Painting processes fully automated and optimized
The Center for Networked Surface and Coating Technology includes a FANUC P-350iA/45 painting robot on a seventh linear axis, with the option of integrating additional robots on the linear axis if required. The installed FANUC P-350iA/45 features a reach of up to 2,600 mm and a payload of up to 45 kg, which is high for painting robots, and is used in particular in the aerospace sector. In order to be able to process higher components, the robot system was installed on a raised steel structure.
The automatic painting booth can be heated, humidified and also used for drying. In addition, fully air-conditioned paint booths are also available at Fraunhofer IFAM in Bremen.
The paint is supplied via a 2K dosing system and, depending on requirements, supplies a wide range of application technology from pneumatic atomizers to high-rotation atomization. Thanks to the quick-change system, atomizers can be changed in a very short time. Solvent-based coatings, waterborne coatings and 2K coatings can be processed here.
Development of chemical-free and environmentally friendly treatments
Flexible adaptation of technologies continue to allow resource and environmentally friendly surface pretreatment and can massively reduce the use of solvents and cleaning media, even eliminating them completely. Furthermore, the wetting and adhesion of more environmentally friendly solvent-reduced paint systems can be significantly improved. Especially in the field of aircraft construction, a pretreatment adapted to the respective material is of great importance for the OEM as well as for the MRO sector.
Automated quality assurance using AV/VR and machine learning
Digital solutions for mobile and inline applications are being developed for quality assurance to safeguard processes and quickly determine material and production data. Here, the focus is on the development of new measurement methods from laboratory application to use under real conditions. The exemplary quality control of aircraft paint assemblies and the superficial paint layer is tested with the help of an inline-capable hyperspectral camera. In the process, the data is analyzed with the help of machine learning.
In order to train via Machine Learning models that are capable of performing automated assessments, annotated data is provided for training. Based on this data, the algorithms independently learn distinctive features by which the applied coatings can be distinguished. The traceability of the algorithmic decision plays a major role here. Random forests and neural networks are available. The former are algorithms that have been in use for a long time and can also distinguish between complex data. Neural networks, on the other hand, have only been used for a short time, but in many cases they can outperform previous models in terms of accuracy and speed, so that even sophisticated, robot-guided inline investigations are possible.
Visualization of measurement data: IoT data structure with variable result visualization
Digitized, inline quality assurance of surfaces enables direct feedback to process control through rapid classification of the recorded data. Thus, on the one hand, process steps can be saved where the desired surface quality has already been achieved, and on the other hand, specifically defined areas can be reprocessed. With the aid of component position recognition and, for example, the projection of results onto the component, direct visual feedback is possible. Another advantage is the variable change of the information depth for the result display, so that, for example, certain user groups (e.g. skilled worker, process engineer) can call up different detail depths of the data via an IoT database.