Reliable identification of cast components
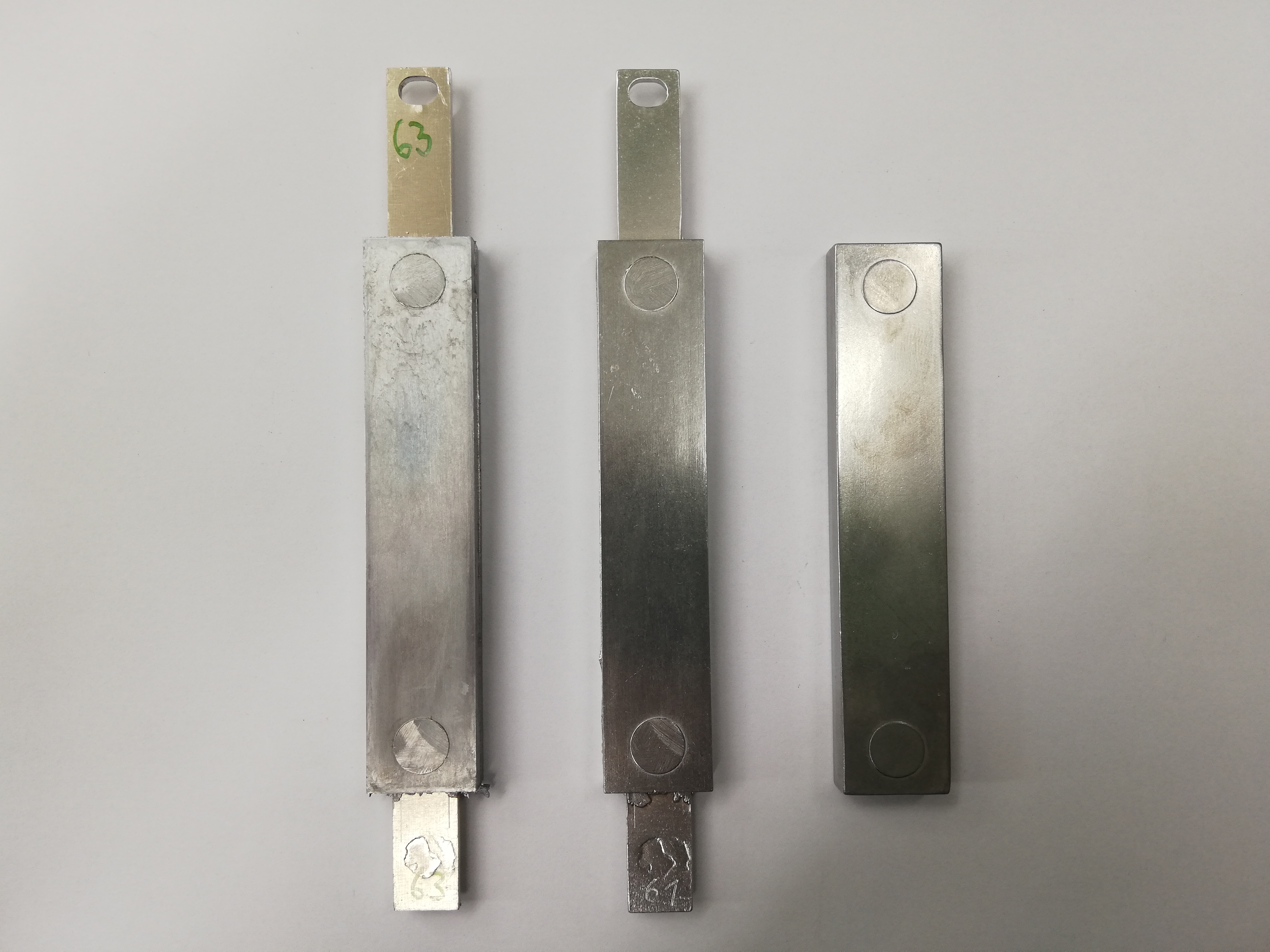
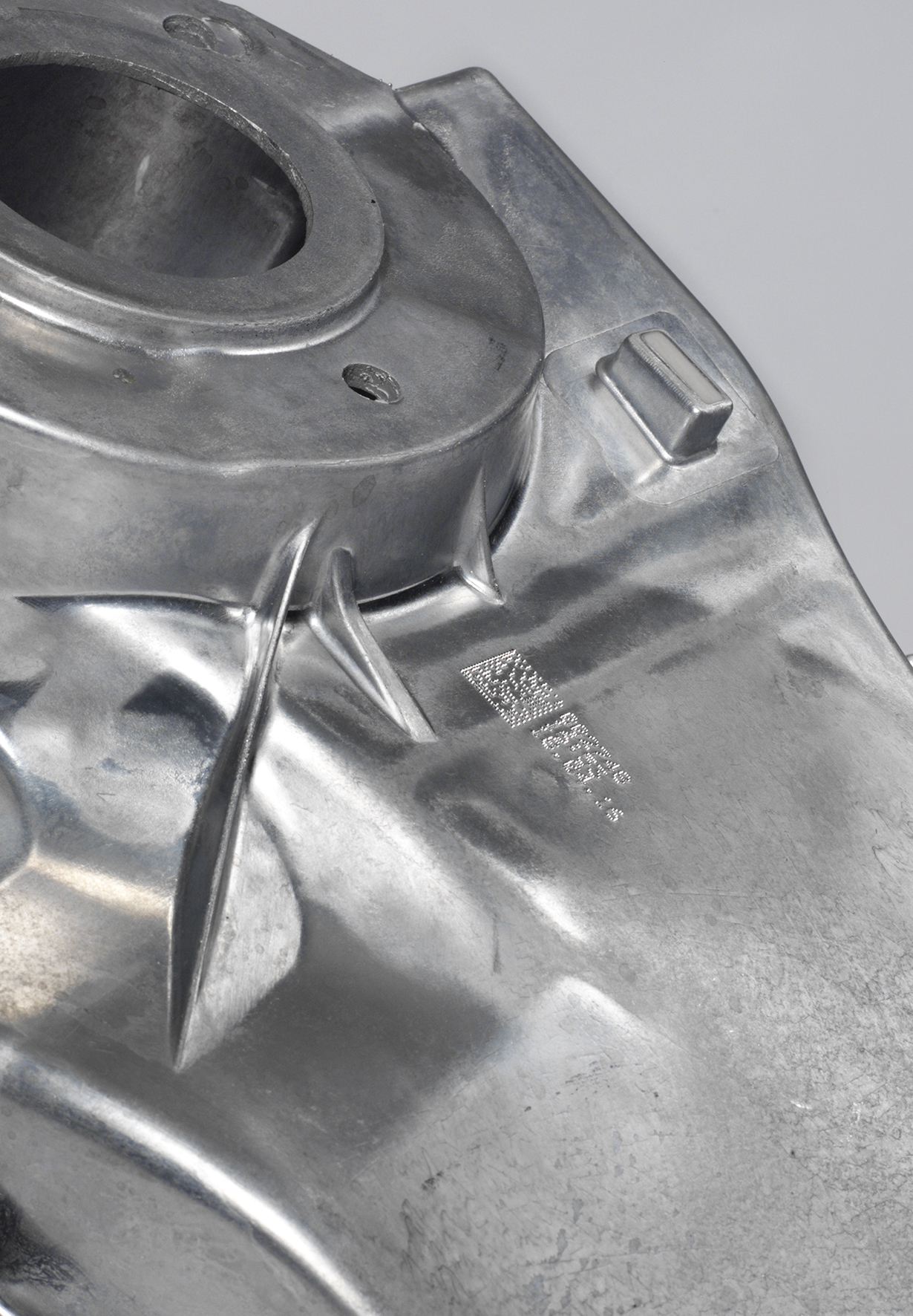
The reliable identification of castings is an attractive goal in many respects. For example, it permits the unambiguous assignment of production parameters to a specific component and thus enables quality documentation, as is increasingly required not only in the aerospace industry. In addition, it forms the basis for process control based on the individual component, as is being pursued in the context of Industry 4.0 approaches.
Cast-in elements for the identification of cast components provide decisive advantages
Classical methods of component identification are usually based on the component surface. The simplest methods work with stickers showing bar or data matrix codes. More reliable are methods that modify the actual component surface. Here, embossing, needle or laser methods are known, among others. In processes which work with lost molds, like sand casting, the transfer of coding from the mold to the component is also practiced - for example in the field of printed sand molds.
What all these approaches have in common is that external influences such as corrosion or superficial mechanical damage can erase the coding. There is also the risk of targeted manipulation. There is no danger of either of these if the identifying element is embedded in the casting and thus cannot be seen or accessed from the outside. Possibilities in this respect include cast-in, e.g. additive manufactured, data matrix codes which can be read by ultrasonic or X-ray methods.
Fraunhofer IFAM offers extensive expertise and capabilities in casting technology
Another option, which is particularly suitable for die casting, is the integration of RFID systems (CASTTRONICS®). At Fraunhofer IFAM, foundations for the implementation of this technology have been laid in various projects, which extend to the automation of insertion into the die casting tool. In addition, solutions have been developed which start from a characterization of the given casting surface instead of a deliberate change and use random deviations on the mesoscale for identification.
This enables our experts to offer a wide range of options for component identification in the field of casting technology. The selection is made depending on the specific product and process in close consultation with the respective customer or development partner.