futureAM – Next Generation Additive Manufacturing
futureAM – Next Generation Additive Manufacturing

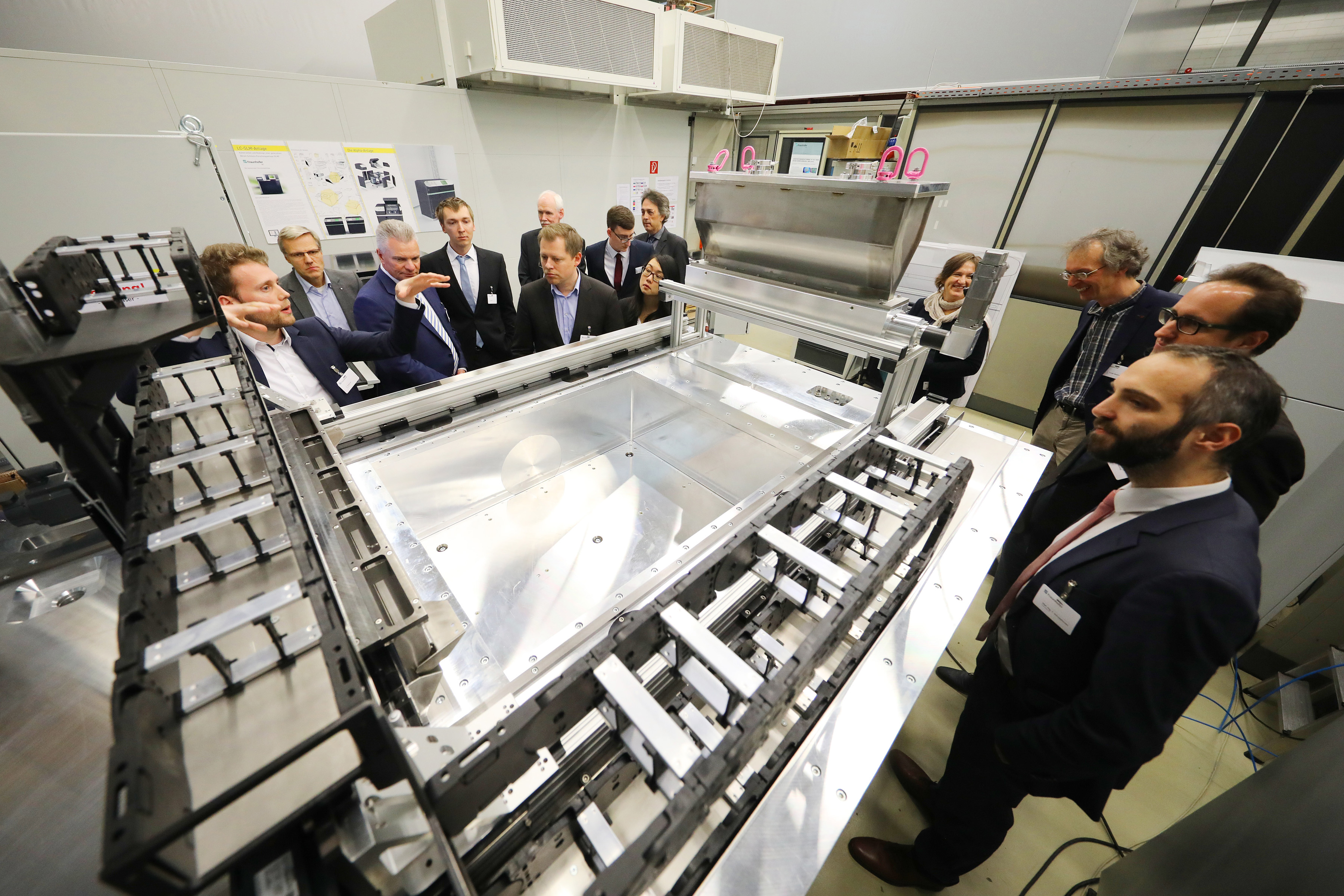
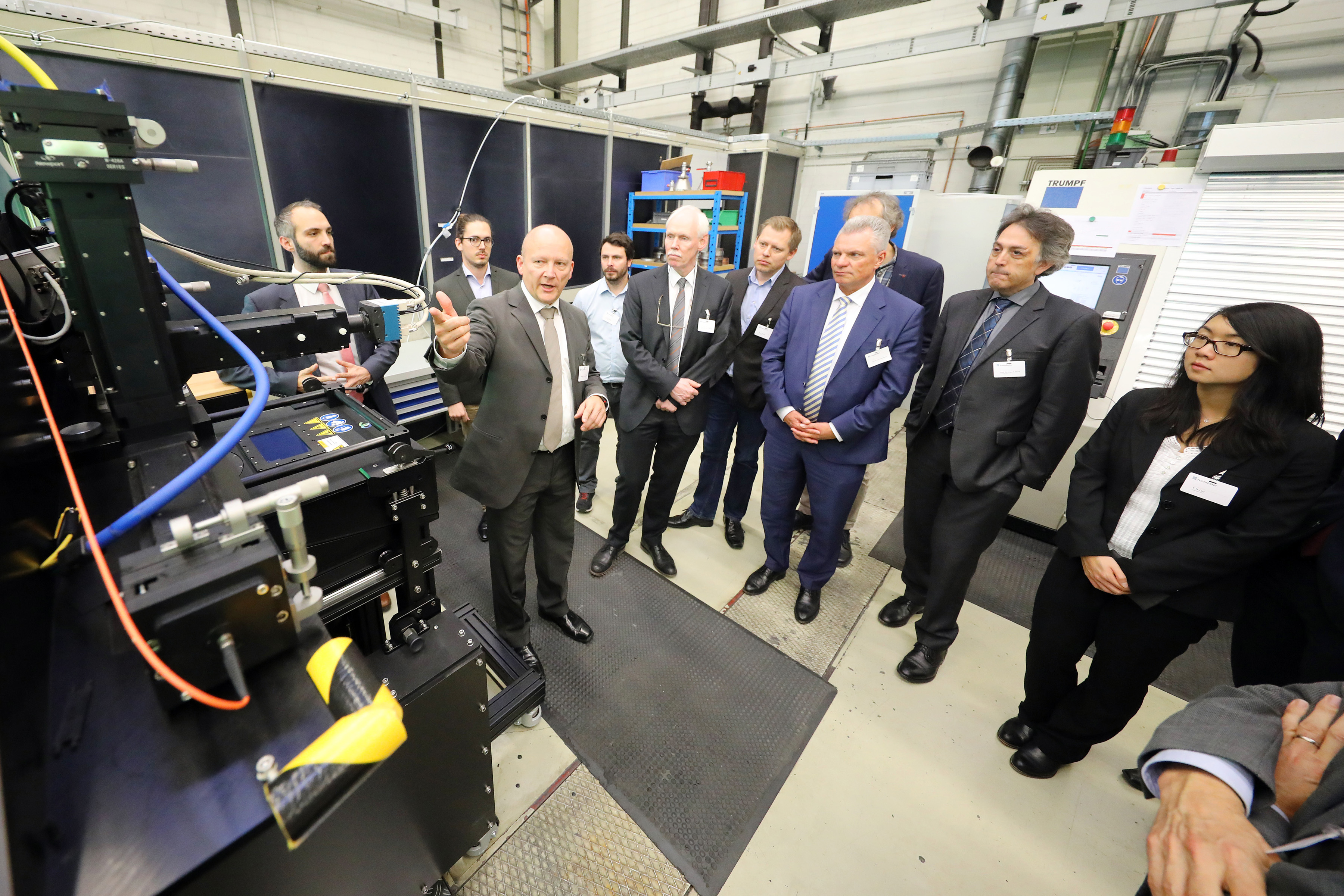
On November 14th, 2017, the Fraunhofer focus project, futureAM, was launched in Aachen under the auspices of the Fraunhofer Institute for Laser Technology ILT. Six project partners – the Fraunhofer Institutes ILT, IWS, IWU, IGD and IFAM as well as the LZN Laser Zentrum Nord – have set themselves a clear goal: Over the next three years, they will work closely together to secure the prerequisites for significant technological leaps in additive manufacturing with metallic materials (metal AM).
The focus project has a concrete goal – to significantly accelerate the additive manufacturing of metal components and, at the same time, reduce manufacturing costs. In addition, it plans to abolish the current limitations of size with the help of new plant design concepts. »The research platform will develop new digital process chains, scalable and robust AM processes, systems engineering and automation, as well as expand the range of processable and affordable materials«, explains Prof. Johannes Henrich Schleifenbaum, coordinator of futureAM and Director of Additive Manufacturing and Functional Layers at Fraunhofer ILT in Aachen.
Cooperation platform strengthens German market position
In many industries there is a world of optimism regarding metal AM. In Germany, the pioneer of this technology, many institutes, universities and young and established companies have been working in this emerging sector of industry for years. They have developed numerous plants and processes for the entire value chain, from material production to plant construction. If only niche applications were in the focus before, now the breakthrough in series production seems to be imminent. But Germany can only maintain and expand its world-leading position if its own research institutions share their knowledge base in the field of metal AM and generate significant technological leaps, which in turn can be taken up by the industry. The project partners have defined four fields of activity in which they plan to secure Germany’s technological edge:
1. Industry 4.0 und Digital Process Chains
2. Scalable and Robust AM Processes
3. Materials
4. System Technology and Automation
Production of demonstrator components in the Virtual Lab
Consortia in the field of 3D printing are not uncommon, but the futureAM platform differs in one point from others: It is characterized by practical relevance, based on many years of experience that the participating institutions have gathered with metal AM. »It is unknown to many that some companies already use additive manufacturing for series production – for example, for the production of dentures, implants or turbine components«, says Prof. Schleifenbaum. »Building on these first pioneering achievements, we are now concerned with implementing and integrating a new generation of metal AM along the entire process chain. The complete digitization of the process chain, new materials, innovative design options and an accelerated production process by a factor of 10 are the objectives«. To this end, the six project partners cooperate in a Virtual Lab with a closed digital map of the competences and equipment of the participating institutes. Every entity – machine or product – is assigned and described a »digital twin«. On the basis of these digital twins, real systems can be optimized by means of modeling and simulation. This is used, for example, for error diagnosis, predictive analysis or product and process optimization. The role of humans is changing, moving away from today's central planning to the decision-making and monitoring. Autonomous systems within the virtual laboratory support the people on location with suitable evaluation and monitoring tools. The Virtual Lab thus provides complete digital transparency.
The Laser Zentrum Nord becomes a Fraunhofer Institute
A common thread in all activities is digital transformation, because the project stands and falls on its success. The LZN Laser Zentrum Nord GmbH of the Hamburg University of Technology (TUHH) will play an important role here as it will be part of the Fraunhofer-Gesellschaft as of January 1, 2018, as the Fraunhofer Institute for Additive Production Technology IAPT. Above all, this Hanseatic institute has made a name for itself by developing complete process chains for small and large companies from a wide variety of industries. They are, therefore, also managing the first field of activity in which Industry 4.0 and digital process chains are the focus.
Expand and use strengths – the futureAM project partners
The scientists of the institutes involved work together in an interdisciplinary manner. They will demonstrate how practical their innovations are on the basis of concrete components. For example, a steering knuckle will be manufactured using the multi-material AM process. The institutes will integrate all of the steps in the entire process chain, from designing or re-designing the component, producing it with the selective laser melting process, setting up the support structures with laser metal deposition technology to removing them automatically and post-processing the component. As coordinator, Fraunhofer ILT in Aachen ensures that scalable and robust AM processes are the result. The LZN Laser Zentrum Nord, future Fraunhofer Institute for Additive Production Technology IAPT, in Hamburg, is responsible for Industry 4.0 and digital process chains; the Fraunhofer Institute for Computer Graphics Research IGD in Darmstadt is also active in this field of activity. The Fraunhofer Institute for Material and Beam Technology IWS in Dresden works together with the Fraunhofer Institute for Manufacturing Technology and Advanced Materials IFAM on a reinforcing structure made of a second high-strength material. The system technology and automation for post-processing of components is the responsibility of the Fraunhofer Institute for Machine Tools and Forming Technology IWU in Chemnitz.
Last modified: