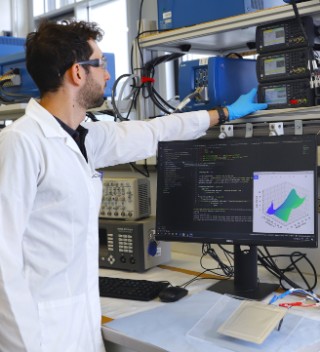
An innovative measurement method enables optimized battery management in electric vehicles, helping to make them safer and extend their lifespans. Impedance spectroscopy from the Fraunhofer Institute for Manufacturing Technology and Advanced Materials IFAM analyzes detailed measurement data on the battery’s state in real time during operation. This means batteries can also be used for safety-critical applications.
more info