Efficient electrodes suitable for mass production for the manufacturing of hydrogen by alkaline electrolysis
The energy carrier hydrogen can be produced very efficiently from renewable energies by electrolysis of water. In industrial electrolysis plants, electrodes with a total area of several hundred square meters are installed. Find out how Fraunhofer IFAM develops and qualifies electrodes suitable for mass production for industry.
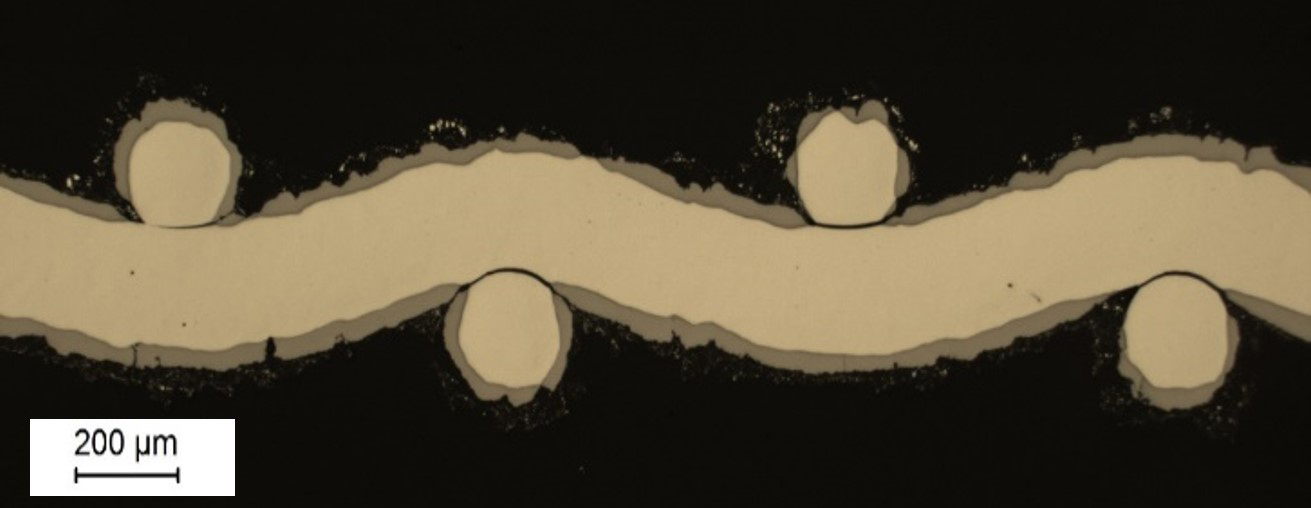
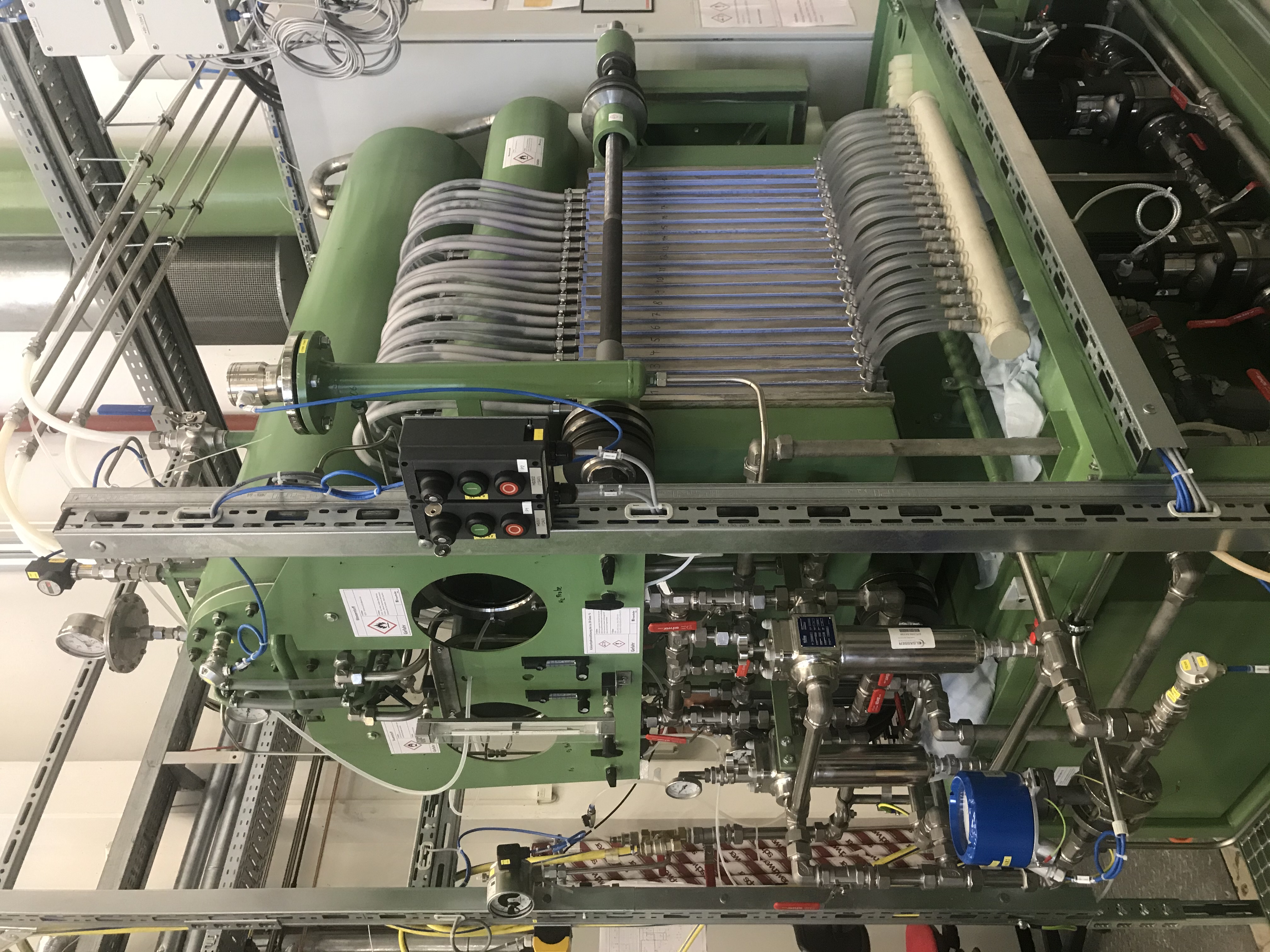
In the context of the energy turnaround and the associated indispensable use of
climate-friendly energy carriers, the Dresden branch of the Fraunhofer Institute for Manufacturing Technology and Advanced Materials IFAM has built up a strong and
visible competence in the field of hydrogen technology over the past years. A thematic focus of its work is the development of materials and manufacturing technologies for electrodes for alkaline water electrolysis (AEL) for sustainable and highly efficient
hydrogen production. Within the framework of several public as well as bilateral
industrial projects, significant progress was made in the areas of electrocatalysts and electrode production.
Currently, alkaline electrolyzers with a single stack capacity of up to 5 MWel are
available on the market. They are being optimized at component level with regard to robustness, space-time yield and flexible operation as well as costs. There are three main development goals:
- Reduction of material costs (no precious metals, no titanium, no critical raw materials)
- Reduction of component costs (more cost-effective production methods and more highly integrated components to reduce the effort of assembling, etc.)
- Improvement of operating parameters (higher current densities)
The quality of electrodes depends on two main factors: firstly, low overvoltage and, secondly, high durability of the electrocatalyst and the electrode structure as a whole. The overvoltage is defined as the difference between the reversible potential (thermodynamic ideal) for the corresponding water splitting reaction Urev and the actually required voltage Ureal, which must be applied for the production of hydrogen or oxygen. The best-known industry values for cell voltages in alkaline electrolyzers are 1.8 to
2.0 V. In general, however, the electrode overvoltage rises with increasing current
density, so that on a technical scale current densities of only 0.3 A/cm² are typically used.
Platinum is naturally the most suitable material for the cathodes on which hydrogen is formed (HER - hydrogen evolution reaction), as it has a very low overvoltage. However, like other precious metals, it is not marketable due to the high material price. Therefore, various cheaper catalyzer materials, which also have a high HER activity (low overvoltage), were developed. Nickel and iron compounds in particular show the best pro-perties here. The most common electrode materials today are Raney nickel and nickel-molybdenum layers. In comparison to smooth surfaces, Raney-like surface layers have a significantly larger electrochemically active surface area for the reaction and an increased structural defect density. Therefore, a comparatively low HER overvoltage can be achieved with the same nominal current density.
The R&D work at Fraunhofer IFAM Dresden has shown that three-dimensional cellular metallic structures (meshes, foams, expanded metals, fiber structures) are particularly suitable as current-carrying electrode substrate materials. These can be coated on the surface with efficient and long-term stable catalysts (Picture 1). This increases the current density and, thus, the space-time yield of the electrolysis process in particular, while at the same time ensuring high long-term stability.
At Fraunhofer IFAM a powder metallurgical process has been developed which allows long-term stable and homogeneous coatings of three-dimensional metal substrates with efficient electrocatalysts based on nickel, nickel-cobalt, nickel-molybdenum or nickel-manganese. Precursors of electrocatalysts are applied as powder onto the cellular substrate in a targeted manner. A complicated, multi-stage heat treatment subsequently leads to diffusion and phase formation processes. The result is the active catalyst layer, which is mechanically strong and electrically conductive and connected to the current-carrying substrate. The specific surface can be further increased by an additional selective leaching.
In addition to the activities for the development of electrode materials and 3D structures for alkaline electrolysis, the department Hydrogen Technology at Fraunhofer IFAM Dresden is also engaged in materials and systems for hydrogen storage by means of hydrogen-solid reactions, e.g. metal hydrides, complex hydrides, hydride composites, MOFs and graphites. Another focus is the field of hydrolysis, i.e. hydrogen production by means of water-solid reactions.
Last modified: