Fire-resistant and bio-based fiber-reinforced composites for structural lightweight design in ships
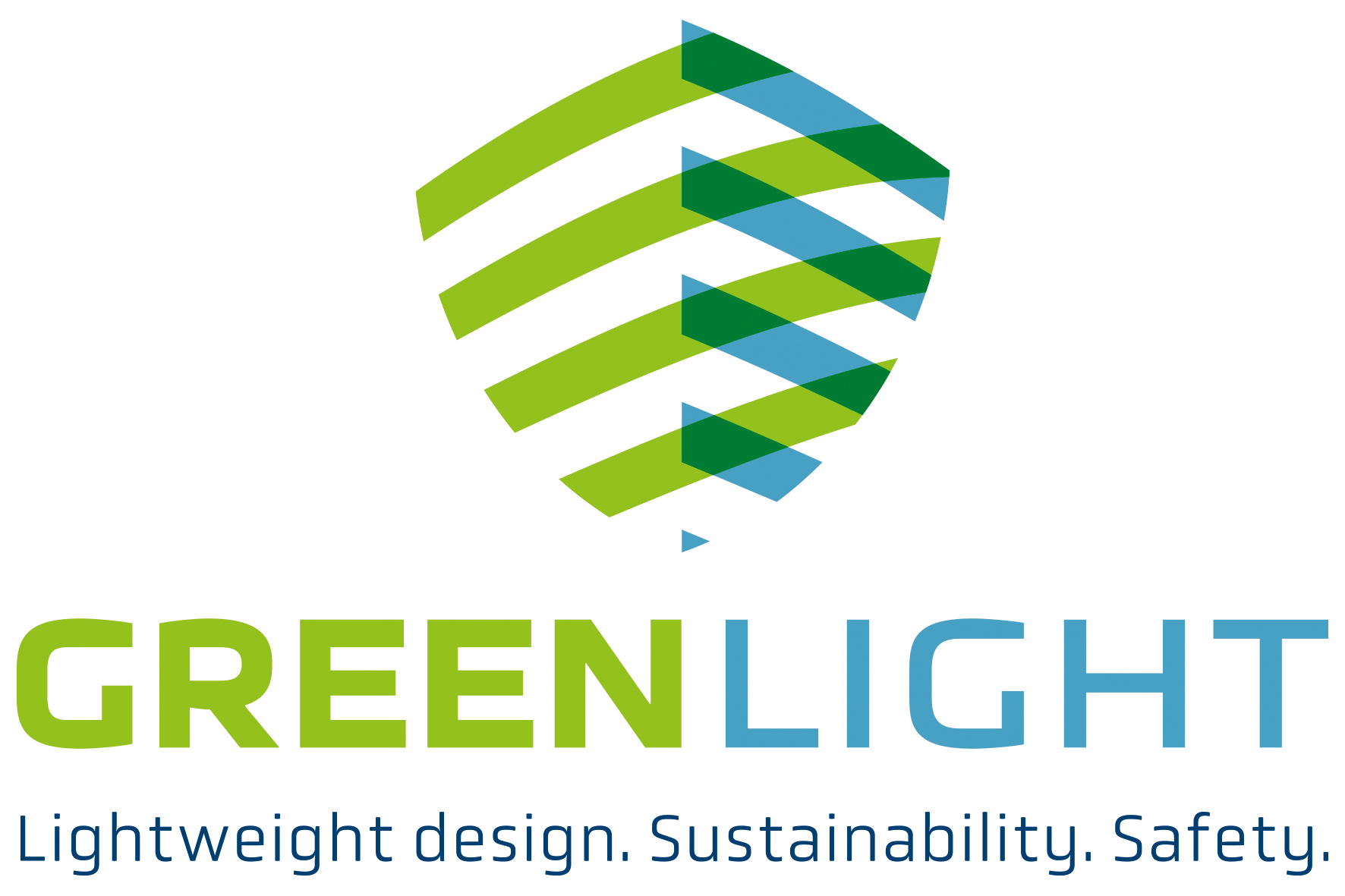
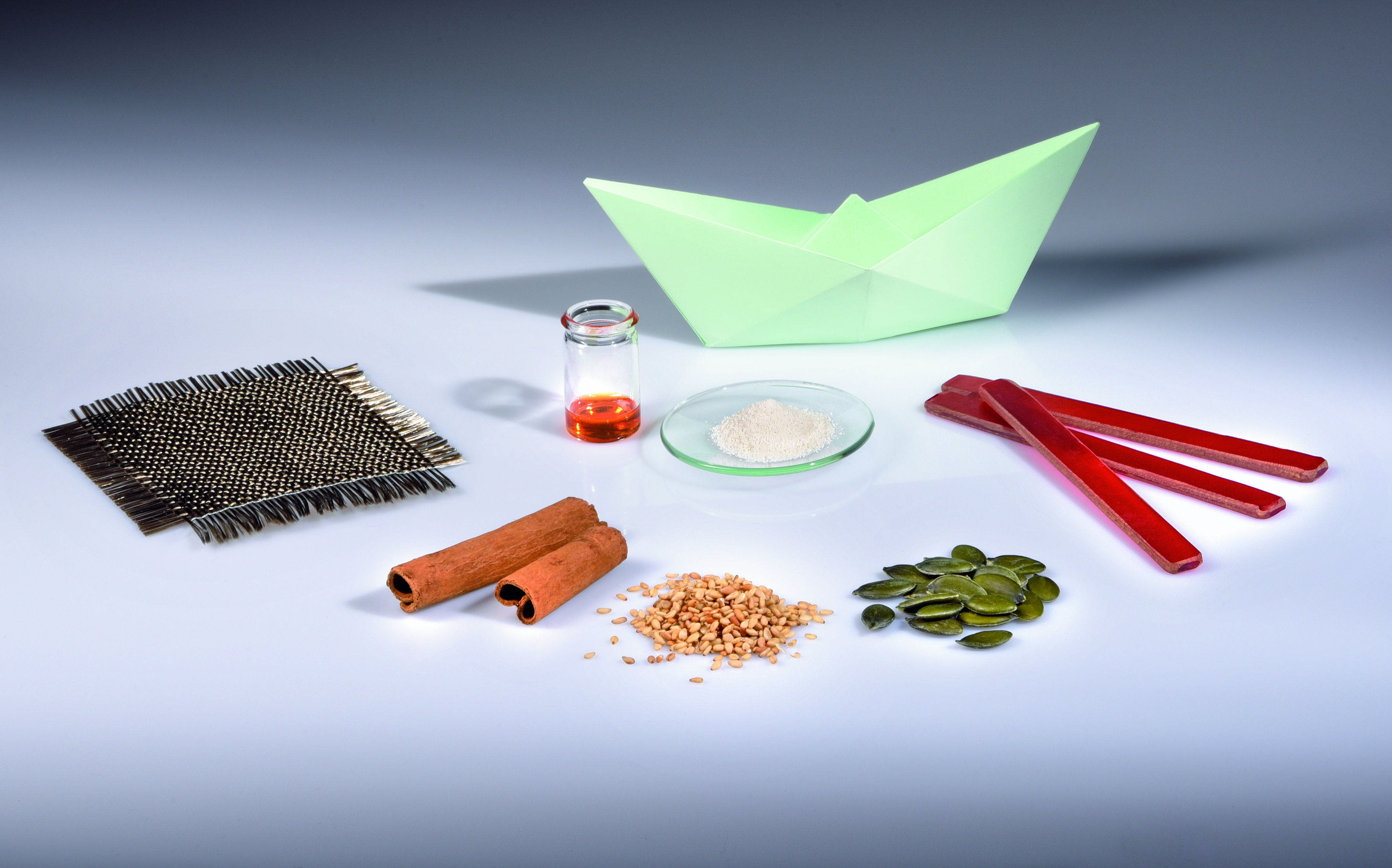
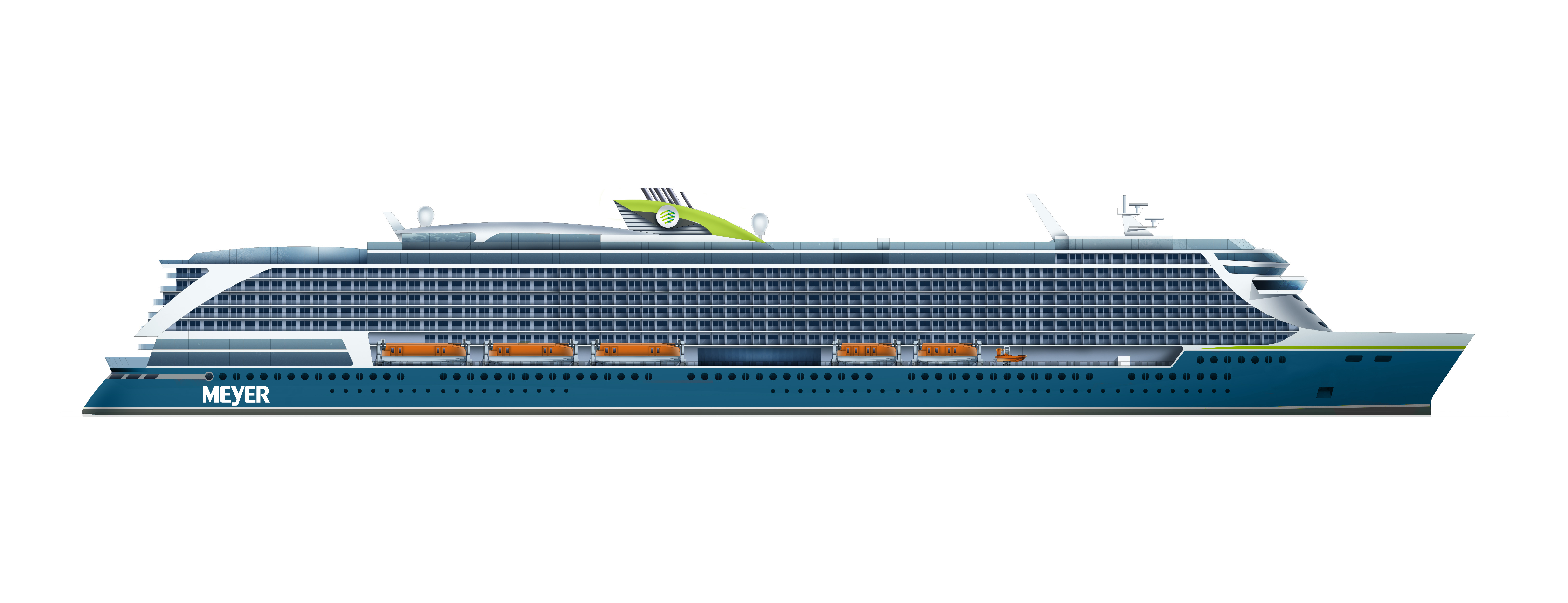
As lightweight construction materials, fiber-reinforced polymers have the potential to improve the ecological footprint of ships. If the fibers and plastic matrix are based on renewable raw materials, the ecological footprint can be further reduced. Integrating these materials as structural components is not state of the art and requires new concepts in shipbuilding. These concepts will have to regard strict safety regulations and fire protection requirements applying to passenger ships. The aim of the "GreenLight" project is to develop bio-based composites with intrinsic fire safety for use in load-bearing structures. The project will also cover manufacturing and recycling concepts.
Due to their lightweight construction potential, fiber-reinforced polymers (FRP) are used in particular in the aerospace and automotive industries and, to an increasing extent, in rail vehicle and boat construction. As a lightweight material, glass fiber reinforced polymers (GFRPs) are cost-effective, corrosion-resistant and can be used to manufacture complex, multi-curved components. However, the situation is currently different in the construction of passenger ships: Steel and, to a lesser extent, aluminum still dominate here, because the necessary approval for use in so-called SOLAS ships (International Convention for the Safety of Life on Sea) has not yet been granted for load-bearing fiber-reinforced polymers. For good reason, passenger ships are subject to stricter safety regulations, which are specified by the International Maritime Organization (IMO) of the United Nations through global standards for the safety and operation of, for example, cruise ships. The "Interim Guidelines for use of fiber reinforced plastic (FRP) elements within ship structures: fire safety issues" lay down the basic requirements for the use of FRP in SOLAS ships. According to the "Interim Guidelines", integrated structures or non-structural parts that do not contribute to the strength of the ship can currently be replaced by FRP.
This is where the "GreenLight" project comes in: Bio-based fiber composites are to be developed for load-bearing components, which at the same time meet the high fire safety standards. Under the leadership of Fraunhofer IFAM, the project partners MEYER WERFT GmbH & Co. KG and INVENT GmbH are contributing their expertise in materials development, manufacturing processes, and shipbuilding. The project is supported by four other associated partners with their experience in materials and semi-finished products as well as the sustainability, approval, and operational safety thereof. Regarding the durability of the materials, further aspects such as dismantling as well as the life cycles of components and materials are already taken into account in the design and material development phase.
Fire-resistant fiber-reinforced composites with potential for structural applications
In FRP components, temperature resistance and fire behavior are highly dependent on the organic polymer matrix. When heat is applied, thermal decomposition of the polymer occurs by pyrolysis processes, in which the decomposition temperature, the gases produced, their flammability and toxicity are significantly influenced by the chemical structure of the polymers used. In order to obtain approval for such a material for SOLAS ships, the high fire protection requirements in particular must be met.
This is where the "GreenLight" project brings in polybenzoxazine-based composite materials. Polybenzoxazines show promising properties with regard to preventive fire protection and are characterized by lower heat release rates, lower smoke gas density and toxicity in the event of fire. Even without the use of halogenated flame retardants, they show great potential to meet fire safety requirements in various applications. With this material-intrinsic approach, the fire behavior of FRPs can meet the requirements even after mechanical deformation of the components due to, for example, collisions or accidents. This approach focuses on structural components in a ship structure for an area of application that goes beyond the state of the art. In this way, further lightweight design potential can be tapped into in the future.
Improving the life cycle assessment through bio-based and sensor-based materials
Against the background of resource scarcity and the drive to increase raw material productivity, raw materials, manufacturing processes and the subsequent recycling of materials play an essential role. FRPs based on renewable raw materials are generally characterized by a lower CO2 footprint over the entire product life cycle compared to conventional, petroleum-based materials.
Based on benzoxazines, chemically, mechanically and thermally stable and even bio-based polymers are accessible. Phenolic components, amines and formaldehydes are required for benzoxazine synthesis, and these components can be obtained from conventional petroleum products, but also from renewable raw materials such as corncobs or sesame seeds. In the "GreenLight"-project, research will be conducted into sustainable benzoxazine-based composites in terms of sustainable chemistry. In this context, special attention will be paid to environmental and social factors in the selection of raw materials (origin, extraction, etc.) as part of a sustainability analysis.
In order to further reduce the CO2 footprint, there is also the task of achieving the longest possible life cycle or service life for these materials. To achieve this goal, the fiber-reinforced plastics are equipped with sensors that allow the condition of the materials to be monitored during operation. With this security, the design of the materials in production can be improved and the number of maintenance cycles as well as the maintenance effort can be reduced.
The sensors can be integrated by inserting film-based or printed sensors in the form of pastes. As part of the "GreenLight"-project, these approaches will be applied to bio-based polybenzoxazines with basalt fiber reinforcement. In addition, concepts will be developed by which data from the sensors can be used for structural health monitoring (SHM). These data also form the basis for a digital twin that maps the material over its entire life cycle (design, creation, operation and recycling) and can be used to evaluate long-term properties.
In particular, the high-performance plastics, such as the benzoxazine-based materials to be researched here, have a high value-added potential as a material upgrading can be reached when they are recycled in alternative applications. Recycling existing materials or even components reduces the use of raw materials. However, this presupposes that the components can be dismantled into materially pure components for further material use. Against this background, the topic of recycling-friendly design concepts for dismantling material composites at the end of life or for a necessary repair during the service life is of importance.
Funding
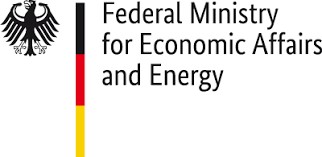
Federal Ministry for Economic Affairs and Energy BMWi
Funding code: 03SX515E
Project Management Organization: Project Management Jülich (PtJ)
Project partners
- Fraunhofer Institute for Manufacturing Technology and Advanced Materials IFAM
- MEYER WERFT GmbH & Co. KG
- INVENT GmbH
Associated partners
- Huntsman Advanced Materials
- Saertex GmbH & Co. KG
- Lloyd´s Register
- nova-Institut für politische und ökologische Innovation GmbH
Download Press release and images
Last modified: