Materials by recipe: powder kit for more flexibility and material diversity in 3D printing
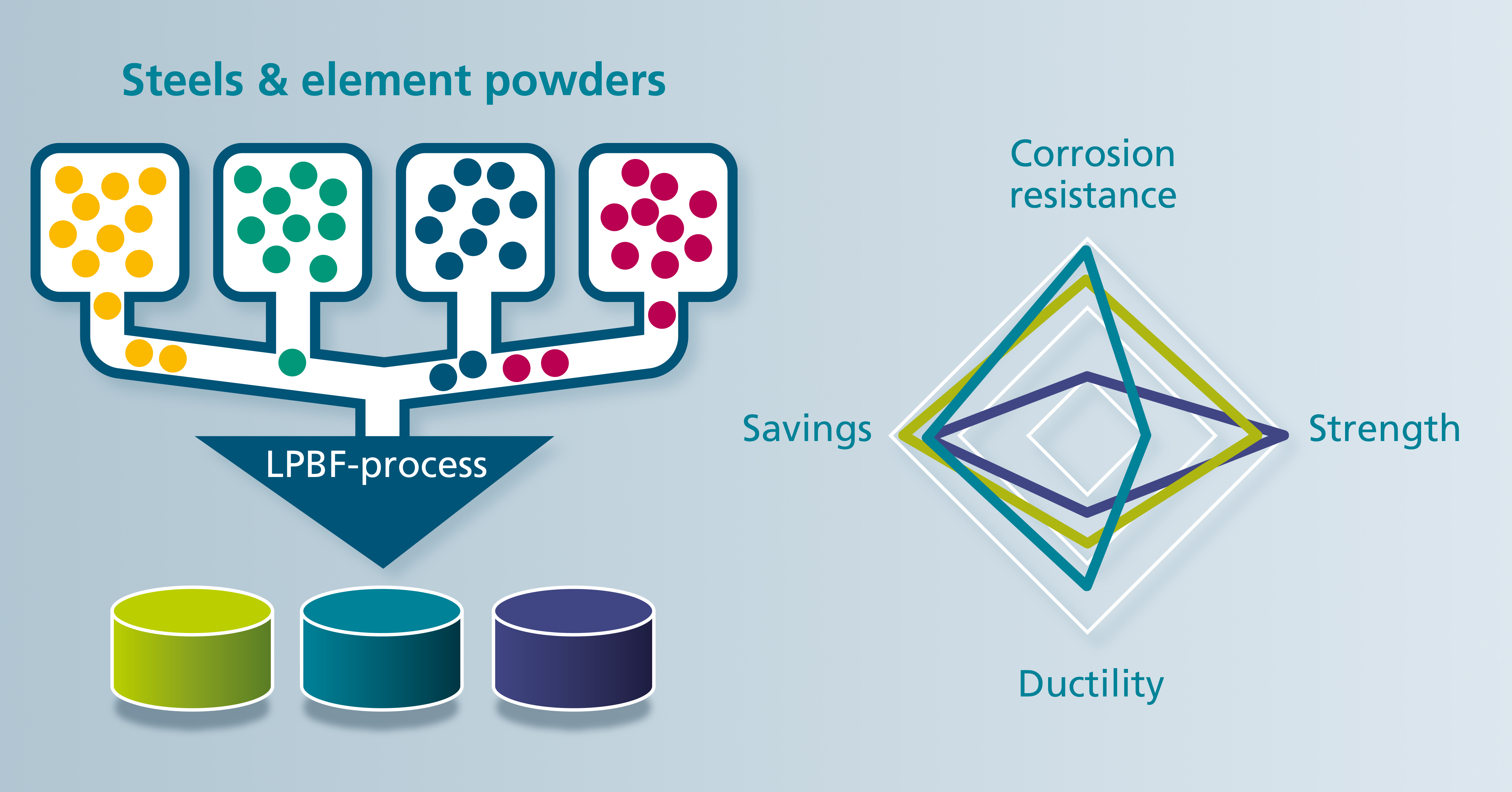
Powder-based laser beam melting (LPPF) is probably the best-known AM process and has great potential for industrial applications. But how can the limited range of materials for this process be circumvented and the market potential further expanded? This question was addressed by the IWM of RWTH Aachen University and the Fraunhofer IFAM in the "LPBF powder kit" project funded by the AiF. The result was the development of a sustainable solution for the individual and robust processing of metal powder blends, so that the user can cover the desired material properties with a small selection of metal powders and flexibly adjust the alloys.
3D printing allows maximum design freedom in the construction and production of components. These advantages have enabled 3D printing technologies to become well established in technical fields such as automotive or aerospace. However, the different fields of application require not only the best possible designed geometry, but also optimized material properties. This requires an appropriately adapted material. However, research into materials for additive manufacturing is still in its infancy. So far, materials that have been qualified by equipment manufacturers for their processes have largely been processed in order to establish the various additive manufacturing processes in the industry. This range of materials is rather small and cannot be compared in terms of diversity to conventional materials, which are mostly produced by melting metallurgy. In conventional, subtractive manufacturing processes, there are hundreds of different steels, aluminum alloys, wear-resistant cobalt-chromium alloys and more for each specific application. In 3D printing, the choice across all metallic materials is limited to less than 30 materials, so not all requirements can be covered.
The right elements ensure a high diversity of material properties
The range of materials can be specifically expanded with the "LPBF powder kit", which consists, for example, of iron base powders with and without carbon, chromium, nickel, molybdenum and titanium carbide. Frequently required material properties include, for example, corrosion resistance, strength, hardness and thermal conductivity. Many steel alloys consist of the same elements such as carbon, chromium and nickel, but differ in their respective proportions. The developed process includes the selection of the alloy composition based on the specific requirement profile of the material, the determination of the powder composition using thermodynamic simulation methods, and powder preparation using adapted mixing and homogenization processes. The optimum process parameters are then determined, and the material is qualified by microstructural characterization and testing of the mechanical properties. Once the powder is mixed, the alloy is created by the subsequent laser beam melting process. The energy of the laser melts the metal powder particles and creates the desired alloy. At the end of the process stands the finished component with customized material properties.
Newly developed corrosion-resistant tool and duplex steels for 3D printing under test
The first concrete application within the project was to produce customized corrosion-resistant stainless steels for specifically adjusted property profiles by alloying in the "LPBF powder kit". During the development work, the influencing factors favoring good corrosion-resistant alloy formation were identified and the quality of the alloy was tested in an application-oriented manner. As a result, it was shown that the corrosion-resistant tool and duplex steels alloyed in the LPBF process are more resistant than the respective base powder and that they have achieved their desired target properties. Another advantage is offered by the possibility of adjusting the microstructure by means of adapted laser parameters. An example of this is the different sizes of carbides in the structure of the tool steels. Depending on the application, different sizes are required. With the developed powder construction kit, these can be efficiently varied and processed into homogeneous components. The results of this sub-project can be made available on request.
Avoiding supply bottlenecks - securing production
Companies that need to be highly flexible and supply different customers with various requirement profiles will benefit in particular from the research project. These include production service providers, most of which are small and medium-sized enterprises. The production of metal powders normally takes four weeks. If a producer wants to cover different materials with small quantities, the waiting times grow enormously. Once the basic materials have been procured, the "LPBF powder kit" can be used to set desired material properties and ensure production in the event of potential supply bottlenecks. Next development steps are the automated calculation and adjustment of the powder mixture for specific product development.
Funding
The work presented was funded in IGF project 20933 N of the Forschungsgesellschaft Stahlverformung e.V. via the AiF as part of the program for the promotion of joint industrial research (IGF) by the German Federal Ministry of Economics and Climate Protection BMWK on the basis of a resolution of the German Bundestag.
Duration: 01.11.2019 - 30.04.2022.
A continuation of the project is intended. Interested companies can participate in the project-accompanying committee of the subsequent research project "Targeted optimization of homogeneity and flexibility in the LPBF powder building kit". Funding for the project is to be applied for as part of the program for the promotion of joint industrial research (IGF) via the Research Association for Steel Forming (FSV).
About Fraunhofer IFAM
Fraunhofer IFAM is one of Europe's most important independent research institutes in the fields of "Adhesive Bonding Technology and Surfaces" and "Shaping and Functional Materials". The focus at all six institute locations is on research and development work with the aim of providing industrial users with reliable and application-oriented solutions.
About the IWM at RWTH Aachen University
The Institute for Materials Applications in Mechanical Engineering at RWTH Aachen University, IWM, was established in 2006 by merging the former Institute for Materials Science, IWK, the Institute for Ceramic Components in Mechanical Engineering, IKKM, and the Lehr- und Forschungsgebiet Werkstoffkunde, LFW. It deals with a wide range of metallic and ceramic materials, their material-specific design application, and the microstructural, fractographic, and mechanical characterization of these materials.
Pictures
© Fraunhofer IFAM, Publication free in conjunction with coverage of this press release.
Download: www.ifam.fraunhofer.de/en/Press_Releases/Downloads.html
Last modified: