How VUV radiation improves the surface properties of silicones
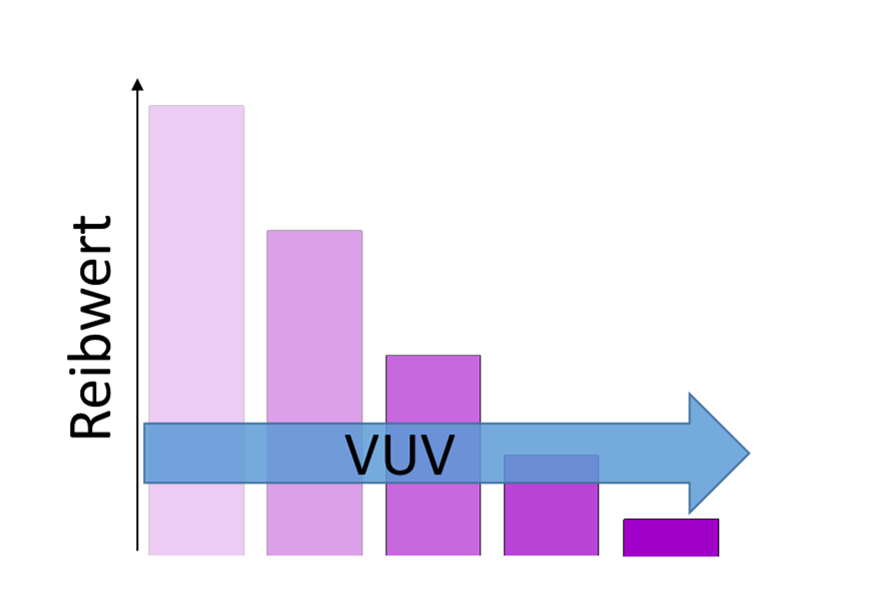
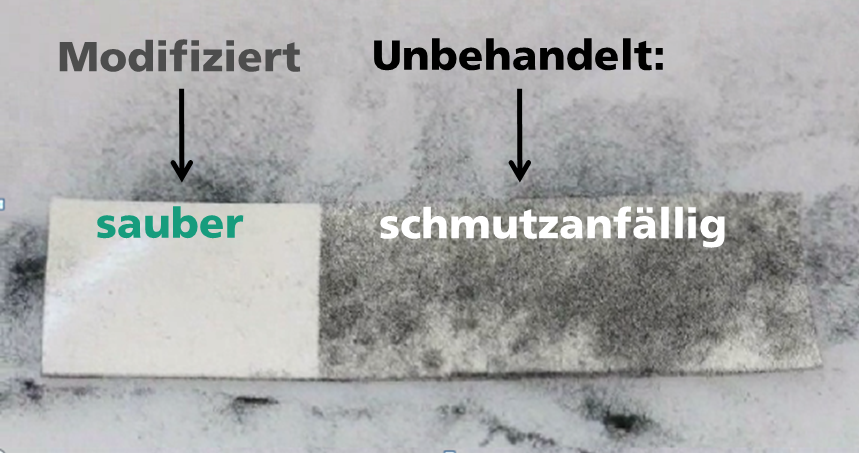
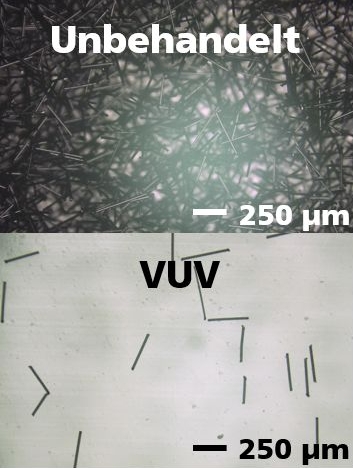
We encounter silicone elastomers in many different areas. Due to their high elasticity, very good temperature resistance and biocompatibility, they are suitable for a wide variety of applications, for example in medical or food technology. The surface properties of the material, on the other hand, are not ideal and make it difficult to use in certain applications. For example, silicones are susceptible to wear, attract dirt, and can only be bonded to a limited extent. At Fraunhofer IFAM, a process has been developed which allows the surfaces to be modified quickly and flexibly without impairing the excellent mechanical properties of the silicones.
Less wear and simplified assembly thanks to low-friction silicone elastomers
Silicone elastomers have very high coefficients of friction, which disadvantageously causes wear and tear, but also makes handling more difficult, for example when assembling silicone O-rings. There is now a simple solution to overcome these problems as the experts at Fraunhofer IFAM have developed SilMoLight®, a low-CoF (low-friction) modification which works on almost all silicone surfaces and gives the silicones greater resistance. The coefficient of friction can be gradually reduced by up to 90 percent. The new approach uses VUV treatment as an easy-to-use technology that involves irradiating the surfaces with special UV lamps (link to VUV technology). The positive mechanical properties of the silicones remain, while the modified surface properties, similar to a functional layer, enable new applications, such as simplified assembly of hoses or rings.
Silicones with dirt-repellent surfaces
Hygiene and cleanliness are essential in many fields of application for silicones. However, due to their high surface tackiness, silicone elastomers are extremely dirt-attracting, which makes them difficult to use, especially in medical and optical applications. SilMoLight® modification makes silicone surfaces not only having lower coefficients of friction but also dirt-repellent. Irradiation with short-wave UV radiation makes the surfaces smoother and harder. This leads to significantly reduced dust and dirt particle adhesion. In addition, the surfaces are noticeably easier to clean. This long-term stable effect has been tested for numerous standard dusts and particles. The material-related advantages of silicones such as:
- No change of the bulk material,
- Elasticity,
- Temperature resistance and
- Biocompatibility
remain unchanged after irradiation. Furthermore, no foreign material is used or incorporated into the silicone (no coating / no fluorine incorporation). The effects mentioned can be generated for almost any silicone surface, for silicone seals, profiles, hoses, O-rings, sheathings and encapsulations as well as silicone molded parts of all kinds. Concrete application examples are: