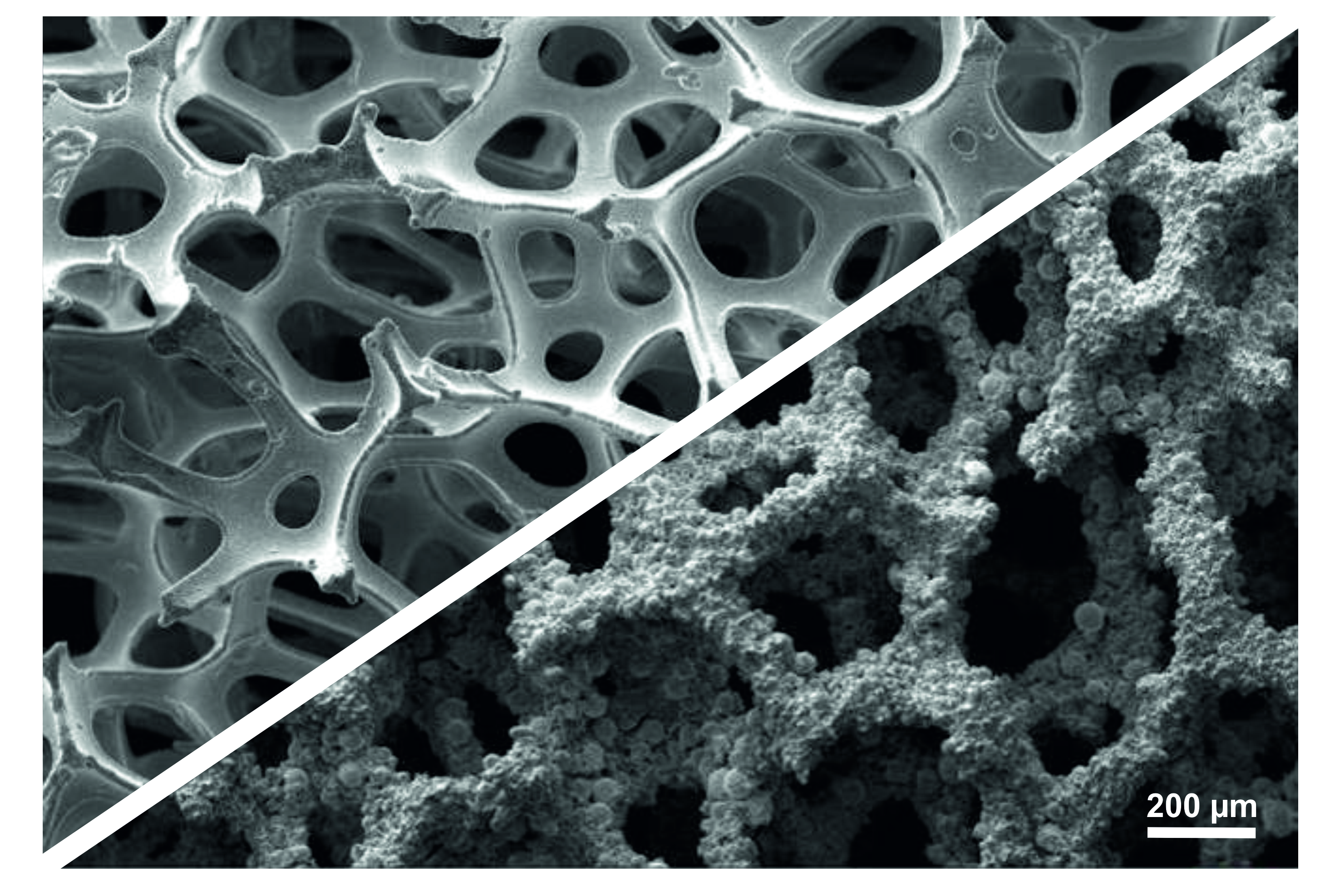
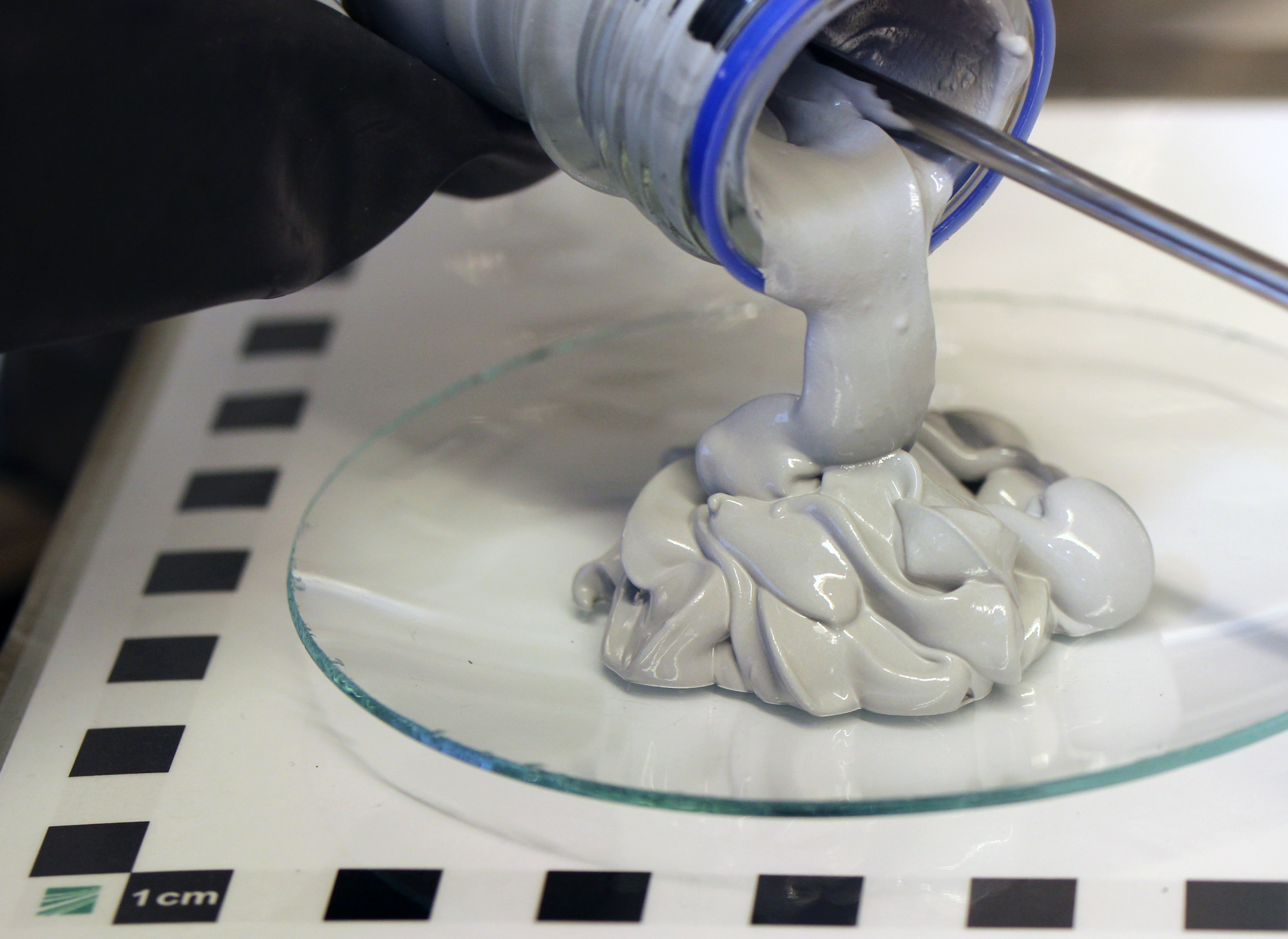
As a versatile energy carrier, hydrogen will play a key role in the long-term success of the energy transition and in climate protection. In addition to climate policy aspects, hydrogen and fuel cell technologies pave the way for many sustainable jobs, new value chains, and a global market worth billions. With this in mind, Fraunhofer IFAM is developing innovative materials, manufacturing technologies, and technical components so that technical systems for the production, distribution, storage, and use of hydrogen can become more efficient, robust, safe, and economical. With the national hydrogen strategy and the European "Green Deal", hydrogen as an energy carrier has moved into the limelight of the energy and fuel transition. New products and services are currently being developed in all places and future value chains for the global hydrogen economy are being established. Fraunhofer IFAM has established itself as a long-standing research and development partner of hydrogen and fuel cell technologies to the great benefit of its customers and clients both nationally and internationally. Our interdisciplinary, cross-scale, and networked approach enables us to lift innovative materials, manufacturing technologies, and technical components from the laboratory environment to an industrial level in a short time. Our development spectrum ranges from hydrogen production, storage and distribution to its conversion into energy or materials, for example in fuel cells. Major challenges are not only the material and manufacturing costs of components, but also their efficiency and durability, in order to arrive at sustainable and economically viable solutions. Current research work on hydrogen and fuel cells at Fraunhofer IFAM is presented below using specific examples.
Hydrogen production
Scalable electrodes for alkaline electrolysis
In the BMBF hydrogen lead project "H2GIGA", Fraunhofer IFAM will be extensively involved in the further development of electrodes for alkaline electrolysis and the scaling of the production route. The manufacturing route addresses in particular the research questions of scalable production, raw material-conserving process steps, and highly active and long-term stable electrodes up to 1.6 meters in diameter.
Seawater electrolysis
The direct electrolysis of seawater has the advantage that the provision of expensively treated water can be dispensed with. However, this technology requires completely new material concepts since the conditions inside the electrolysis cell are highly corrosive. Components of seawater electrolyzers (electrocatalysts, anion exchange membranes, coatings for bipolar plates, etc.) are being developed at the Dresden and Bremen sites of Fraunhofer IFAM. On the one hand, these activities are embedded in the BMBF project "H2 Mare" and on the other hand in the initiative "Innovationswerkstatt Meerwasserelektrolyse" of the state of Bremen.
Titanium paper as current collector for PEM electrolyzers
As part of an IGF research project, a so-called sintered paper made of titanium has been developed in cooperation with the the hydrogen and fuel cell center ZBT GmbH and the Paper Technology Foundation PTS for use as a power distributor in PEM electrolysers. A highly filled medium is produced from fibers and fillers by means of a sheet formation process and further processed into a sintered semi-finished product. The sintering process produces a purely metallic porous titanium sheet, which has been tested in electrolysis cells as a current distributor. It was shown that this technology, which is suitable for mass production, can achieve a performance comparable to a price-intensive benchmark product made of titanium fibers.
Transport and infrastructure
Fraunhofer IFAM will be involved in the "Helgoland Implementation Project" of the BMBF's hydrogen lead project "TransHyDE", where the focus will be on the use of unique material test stands on Helgoland and material development and testing for LOHC tanks (LOHC: Liquid Organic Hydrogen Carrier). Other contents include the development and testing of sustainable corrosion and fouling protection concepts for the protection of offshore structures for the production and transport of hydrogen. Fraunhofer IFAM is also a member of the AquaVentus funding association and, with the Test Center for Maritime Technologies, is actively involved in the development of concepts for the reliable operation and safe maintenance of infrastructure in maritime environments.
Storage of hydrogen
Metal hydrides are solids which can be used in various applications such as sorptive hydrogen storage or thermochemical hydrogen compression. The aim of Fraunhofer IFAM is to develop metal hydride systems for commercialization. Compared to conventional technology, which often uses highly porous hydrides in the form of granules or powders, advanced metal hydride composites consisting of the hydride-forming metal alloy and secondary auxiliary materials such as graphite and/or polymers are used. These secondary materials ensure that the composites can retain their shape as well as increase the reaction kinetics over their lifetime, resulting in greater economy.
Cryogenic hydrogen tanks
For the aerospace sector, hydrogen is usually stored in liquefied form at extremely low temperatures of up to -253°C. Since weight plays a decisive role in these areas, typical lightweight materials, e.g. carbon fiber reinforced plastics (CFRP), are to be used in the future. To make this possible under the extremely low temperatures and to ensure impermeability to the extremely small hydrogen molecule, Fraunhofer IFAM is working on the development of special barrier coatings as part of a "Cryocoat" project funded by the BMWi and led by DLR. Extreme temperature conditions - coupled with repeated temperature changes - place high demands on the resistance of lightweight materials. Together with partners from the aerospace industry, we are developing and using test methods for composites and bonded structures that map different types of stress under cryogenic conditions.
Coatings against hydrogen permeation of pressure tanks
As the smallest molecule or atom, hydrogen has the special property of being able to diffuse through solid materials. In polymer materials, this can lead to significant losses of hydrogen. For the production of hydrogen pressure tanks based on fiber composite technology, bottle-like hollow bodies - so-called liners - are often used, which are wrapped with impregnated continuous fibers in a winding process, enabling them to permanently withstand pressures of 700 bar. If the liners are to be mass-produced from plastic at low cost, the problem of increased hydrogen diffusion of these materials must be addressed. An innovative bottle liner based on vapor phase deposition has been developed at Fraunhofer IFAM. This novel process allows the interior of bottles to be coated with metals which provide an excellent hydrogen barrier. In this way, the pressure tanks can be provided with a metal coating from the inside before or even after the winding process, which improves the barrier properties against hydrogen in such a way that the pressure tanks can be used in closed environments such as in vehicles.
POWERPASTE - Hydrogen storage solution for small vehicles & more
One of the greatest challenges of hydrogen technology is the safe provision of hydrogen at the point of use. The elements of hydrogen logistics, refueling infrastructure, but also hydrogen storage play a key role here. POWERPASTE - a patented invention of Fraunhofer IFAM - is a novel hydrogen storage material based on the light metal hydride MgH2, which enables the use of hydrogen when one or more of these elements are missing or uneconomical for an application. POWERPASTE can be filled into cartridges and release hydrogen in a hydrolysis reactor by dosing the paste and adding water. By means of a suitable reaction control, hydrogen is released as required, i.e. only as much hydrogen is produced as is needed at any given time - for example by a PEM fuel cell. The technology, which is being further developed within the framework of BMBF and BMWi projects, as well as industrial projects, can be used to create power generators for mobile applications, e.g. range extenders for light vehicles, as well as emergency power systems. At the Fraunhofer Project Center for Energy Storage and Systems ZESS in Braunschweig, under the project management of Fraunhofer IFAM, a POWERPASTE synthesis plant is currently being set up at pilot plant level for an annual production of four tons.
Energy converter
Adhesive bonding of bipolar plates for fuel cells
Fraunhofer IFAM provides specific research services in the context of hydrogen technology, from material selection and process development to material analysis, for the realization of bonded joints and their qualification. For the qualification of adhesives and locally applied sealants, we offer compression tests and pressure tests with adhesively joined bipolar plates specially developed for fuel cell technology. In these tests, the adhesive bond or seal must not exceed a previously defined maximum leakage rate for air, helium, hydrogen or cooling medium under various temperature and pressure scenarios. For bonding the bipolar plates, Fraunhofer IFAM has various dispensing systems which can be used in combination by means of a 3-axis coordinate table or a 6-axis robot and can reproduce production scenarios close to the process.