New technologies for hydrogen tanks, fuel cells, batteries and e-motors
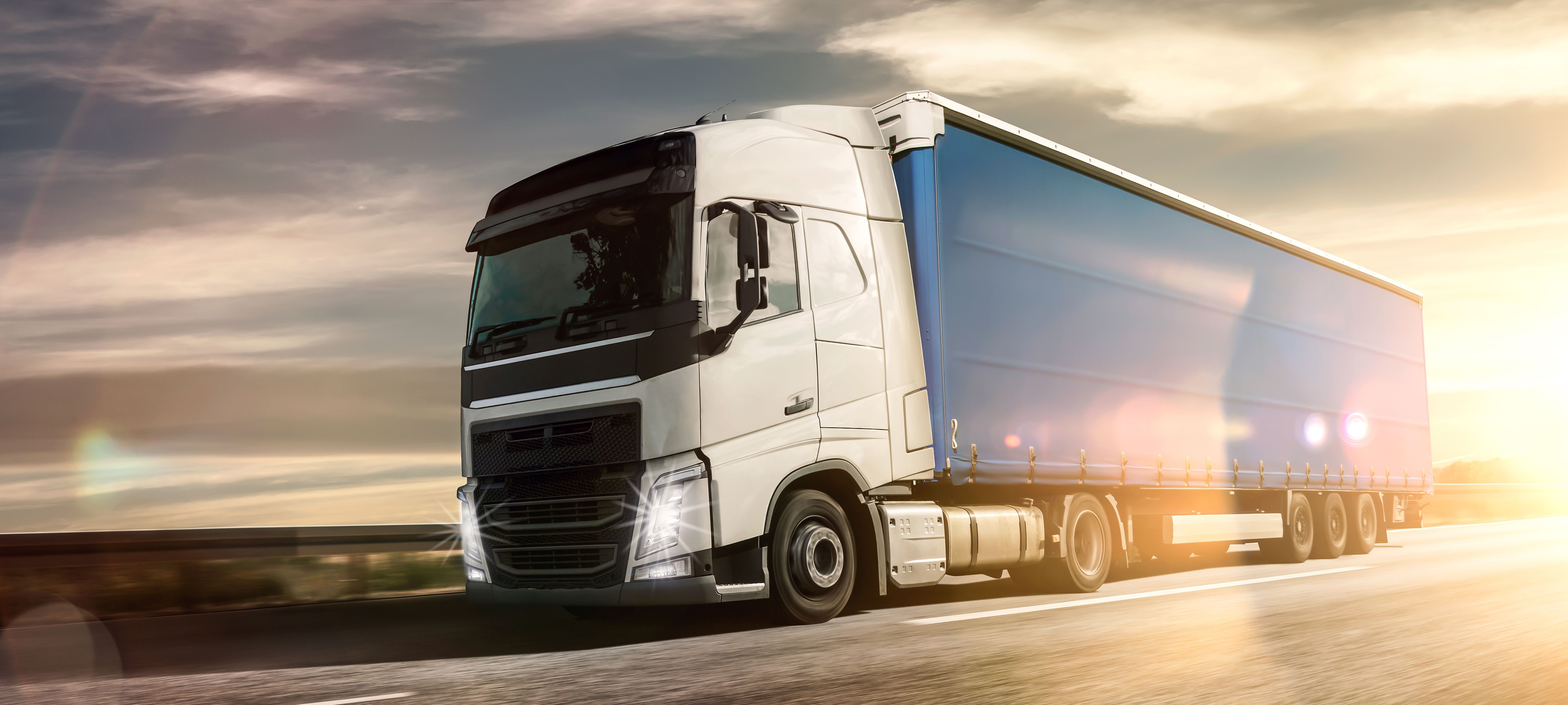
Electrification is the key to CO2 reduction in the mobility sector. The technologies required will be as diverse as the way people move around the world. This is because the powertrain requirements for cars, trucks, trains, ships or aircraft vary. Fraunhofer IFAM has developed new materials and manufacturing processes for the construction of hydrogen tanks, fuel cells, batteries, and e-motors in order to store the drive energy — electricity, hydrogen or synthetic fuel — and then convert it into mobility with different drive variants.
From hydrogen to electricity
Hydrogen storage tanks and fuel cells are needed to convert hydrogen into electricity in vehicles and aircraft. When it comes to the tanks used, the highest priority is given to safety and leak tightness. As a result of this, the institute is developing novel tank designs made of fiber-reinforced plastics (FRPs), as well as specific coatings and methods for testing leak tightness. FRP is being used with a view to conserve energy and resources through lightweight construction from recyclable plastics. The coatings prevent the permeation of the hydrogen molecule into and through the tank material. To this end, the institute has developed a barrier coating for FRP tanks for hydrogen storage at room temperature or under cryogenic conditions. For the marine and aviation industries, work is currently examining the various construction methods and coatings of tanks in order to meet the necessary requirements.
In the production of fuel cells, so-called stacks consisting of several hundred sequences of membrane electrode units and bipolar plateshave to be connected. Adhesive bonding technology can be used advantageously for joining and sealing. A particular challenge is the tightness and durability required for subsequent series production in combination with the speed of the joining process. Current work focuses on the disassemblability of the bondings for the purpose of repairing and recycling the raw materials from the fuel cell.
Batteries for the mobility of tomorrow
The demand for efficient electrical energy storage systems is currently increasing rapidly. Theaim here is to achieve particularly high energy and power densities while at the same time ensuring that the batteries have a sufficient service life. In order to meet these requirements, the institute is researching solid-state batteries in particular. These do not contain flammable electrolyte components, have no flammable liquid electrolytes and promise higher energy densities as well as shorter charging times.
Efficient and powerful e-motors
When it comes to future e-motors, the institute is particularly concerned with the “design for manufacturing” of e-drives to ensure an optimal combination of materials and manufacturing processes, as well as simultaneously pursuing the improvement of the efficiency of e-drives. Current research addresses, among other things, the magnetic properties of electrical sheets: On the one hand, optimizations are being achieved through requirement-based design and innovative materials, and on the other hand, additive manufacturing is being tested as a flexible manufacturing process. The institute has also developed casting technologies for integrating cooling channels into the electric motor housing and coils. This significantly improves heat dissipation and efficiency.