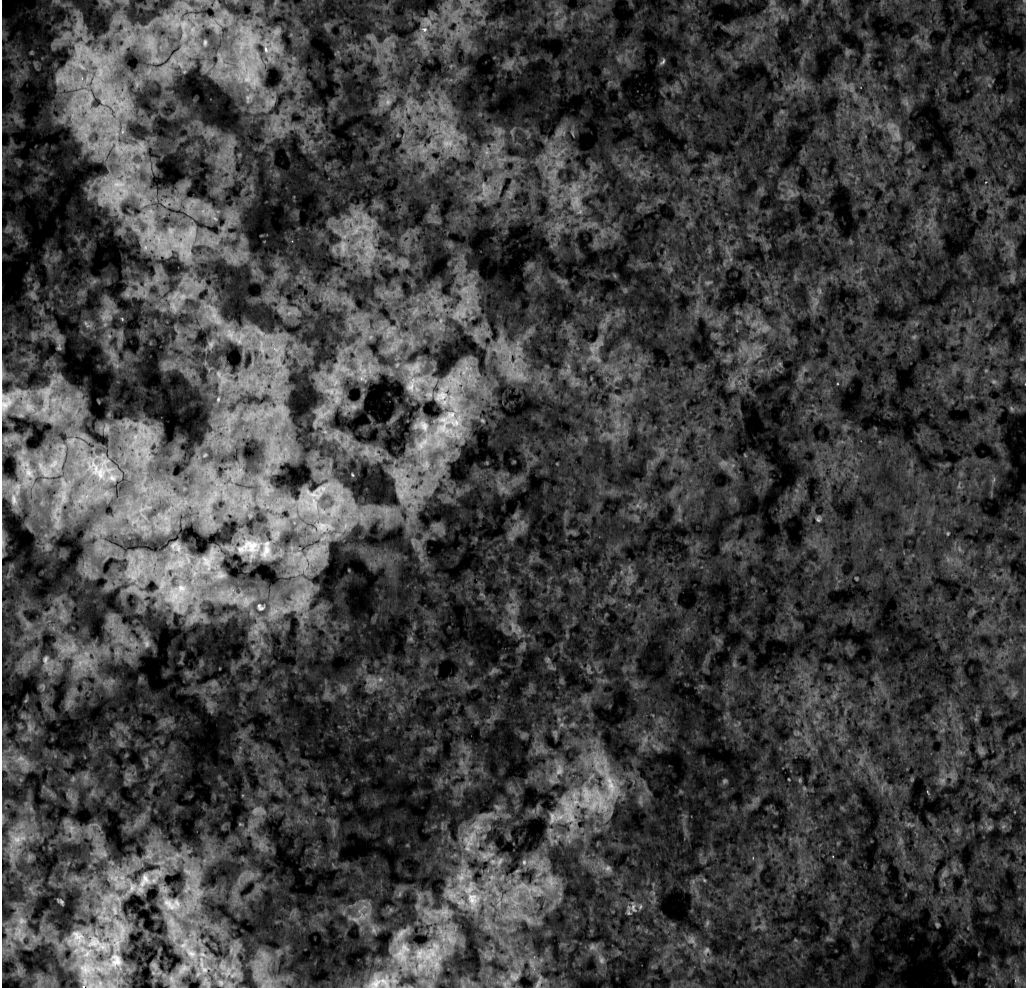
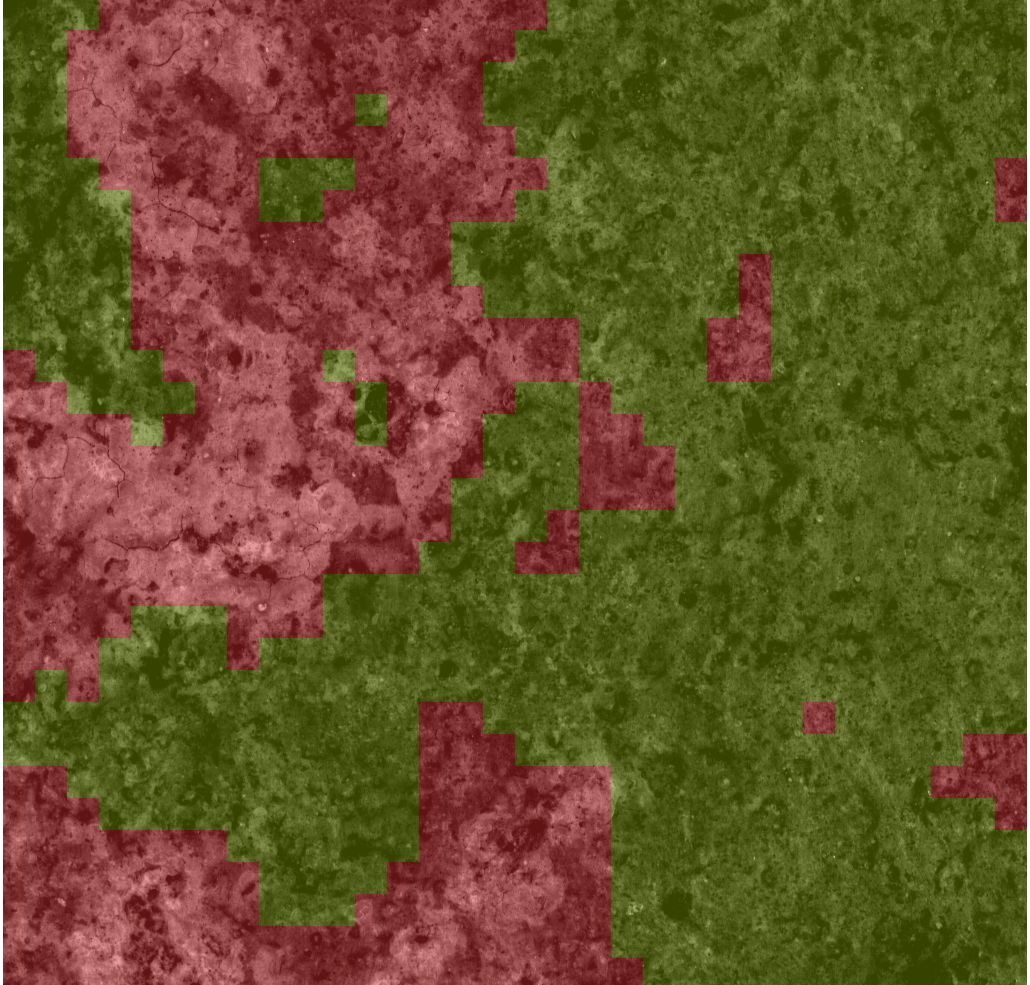
Manual inspection processes for quality assurance are often opposed to an economic optimization of process steps. The use of artificial intelligence and machine learning can overcome these hurdles and significantly increase the quality of the end product as well as the production speed. In addition, knowledge-based algorithms enable targeted knowledge transfer to support employees as well as new digital business models.
The visual inspection of surfaces or components is an important process step within the framework of quality assurance and is carried out by experienced specialists, such as certified inspectors. However, despite the qualification of the inspectors, the inspection result is often subject to a subjective impression, is not reproducible and thus causes unnecessary downtimes.
AI-based solutions
The use of automated image acquisition systems and AI-based algorithms provides an innovative solution to this problem. One algorithm that has been increasingly used in the field of machine learning in recent years is the random forest algorithm. This can be efficiently trained with a few images from an expert and then uses various features to form so-called decision trees, which are used to emulate expert decisions. These trained decision trees are stored in a database and used to evaluate unknown images. The evaluation can even be performed live in the process at high speed. Additional errors or false positives can be added and adjusted at any time by simple retraining. In addition, this algorithm offers clear advantages over neural networks, for example, in terms of the traceability of the evaluation.
Automated assessment for maritime steel construction
Fraunhofer IFAM researches and develops appropriate algorithms for adhesive bonding and surface technology and makes them available to its customers as innovative products. The customized solutions allow manufacturing processes to be optimized economically and the production speed and quality of the end product to be significantly increased. In the current "WindsurfAce" project, this type of data evaluation is being used in maritime steel construction for surface assessment prior to the application of anti-corrosion coatings. The high quality requirements, such as for foundations of offshore wind turbines, can thus be ensured.