Real-Time Measuring Method Extends Lifespan and Enhances Safety of Batteries
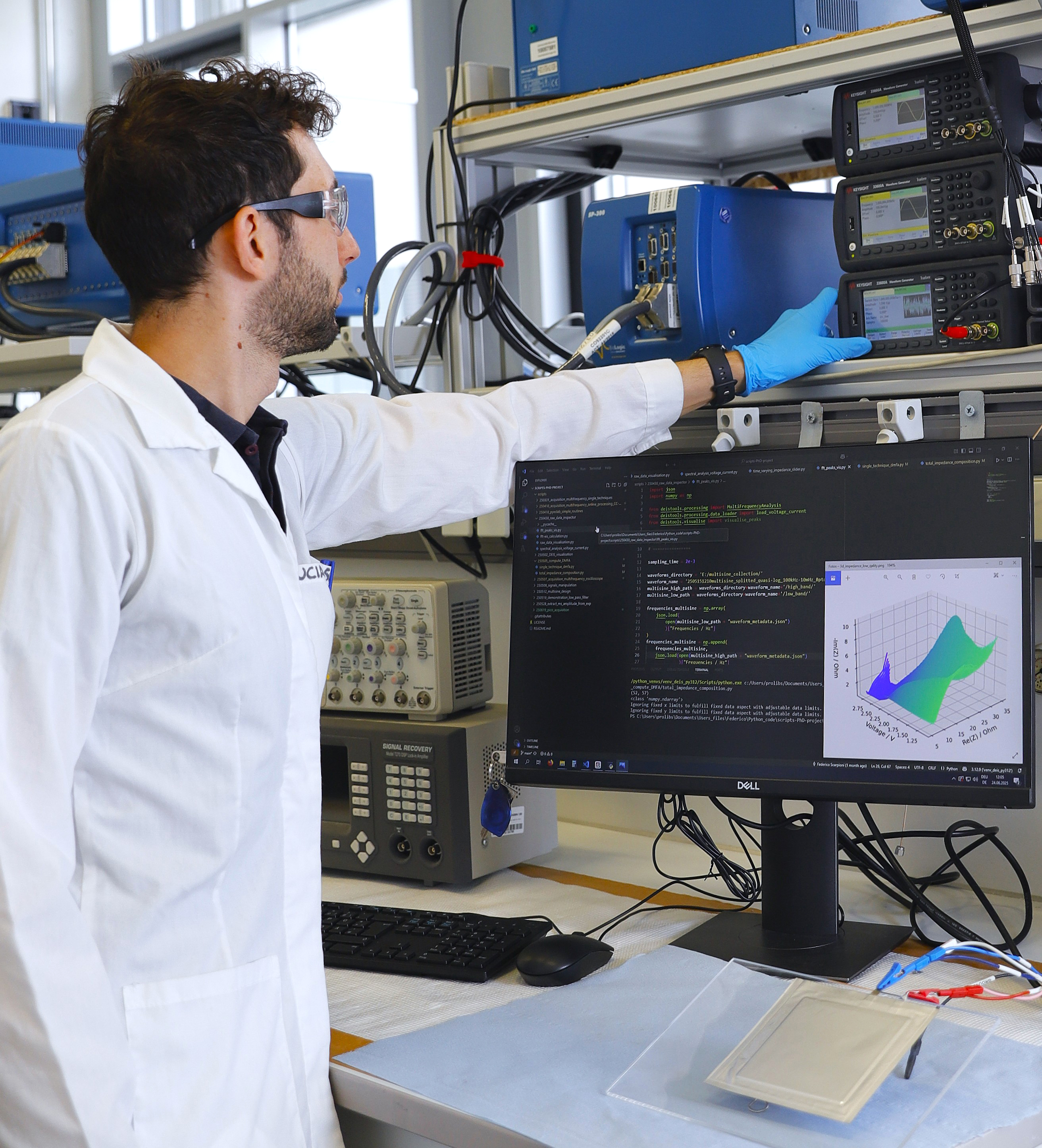
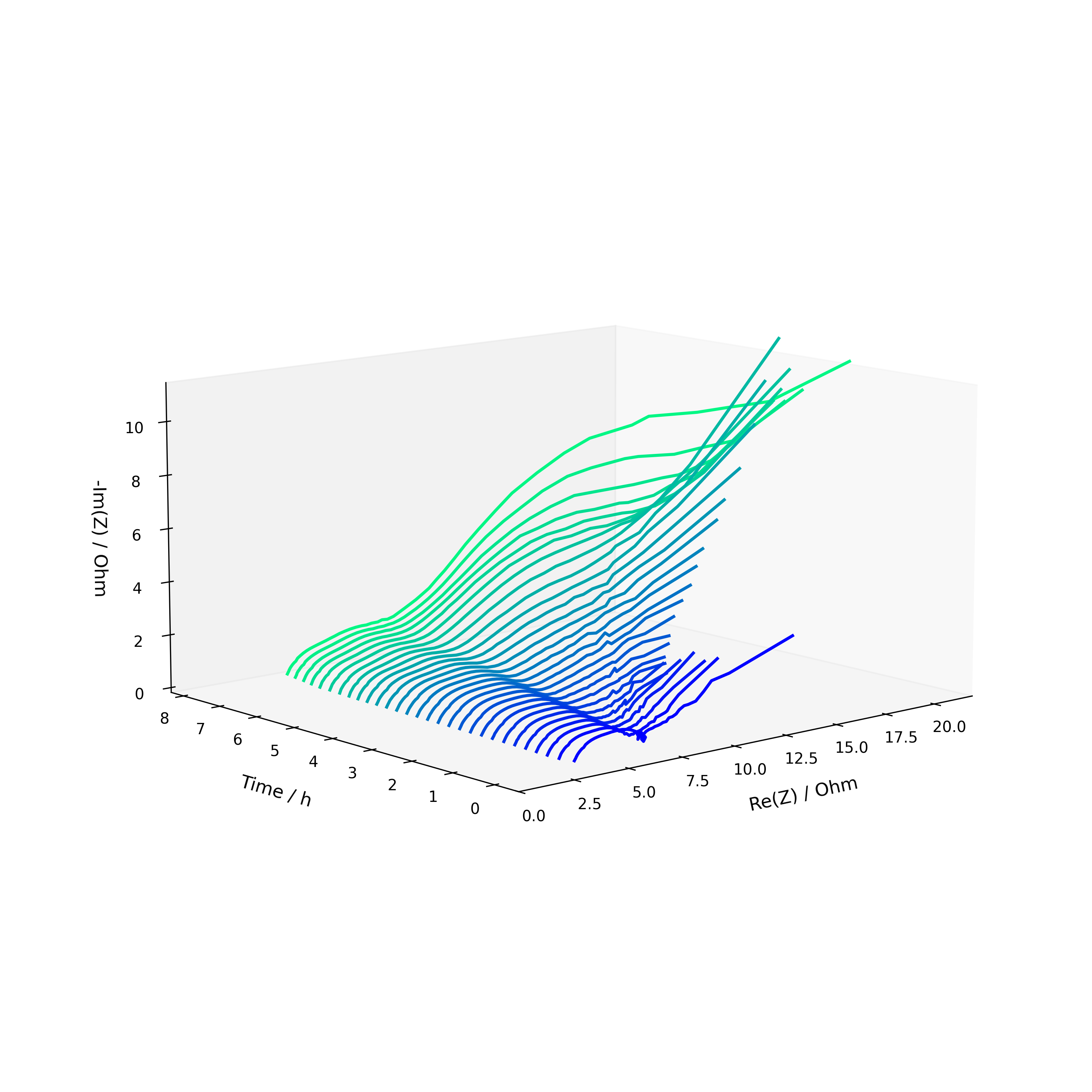
Download
Lab setup for computer-assisted real-time measurement of impedance in a lithium-ion battery cell to analyze its state.
© Fraunhofer IFAM
The graph shows how the curves change dynamically during a charging cycle. The curves provide information on the physical and chemical processes taking place inside the battery cell.
© Fraunhofer IFAM