InnoTrans 2022 – Mobile cleaning and disinfection robot frees rail vehicles from dirt & pathogens
Service robotics from Fraunhofer IFAM in Stade, Germany
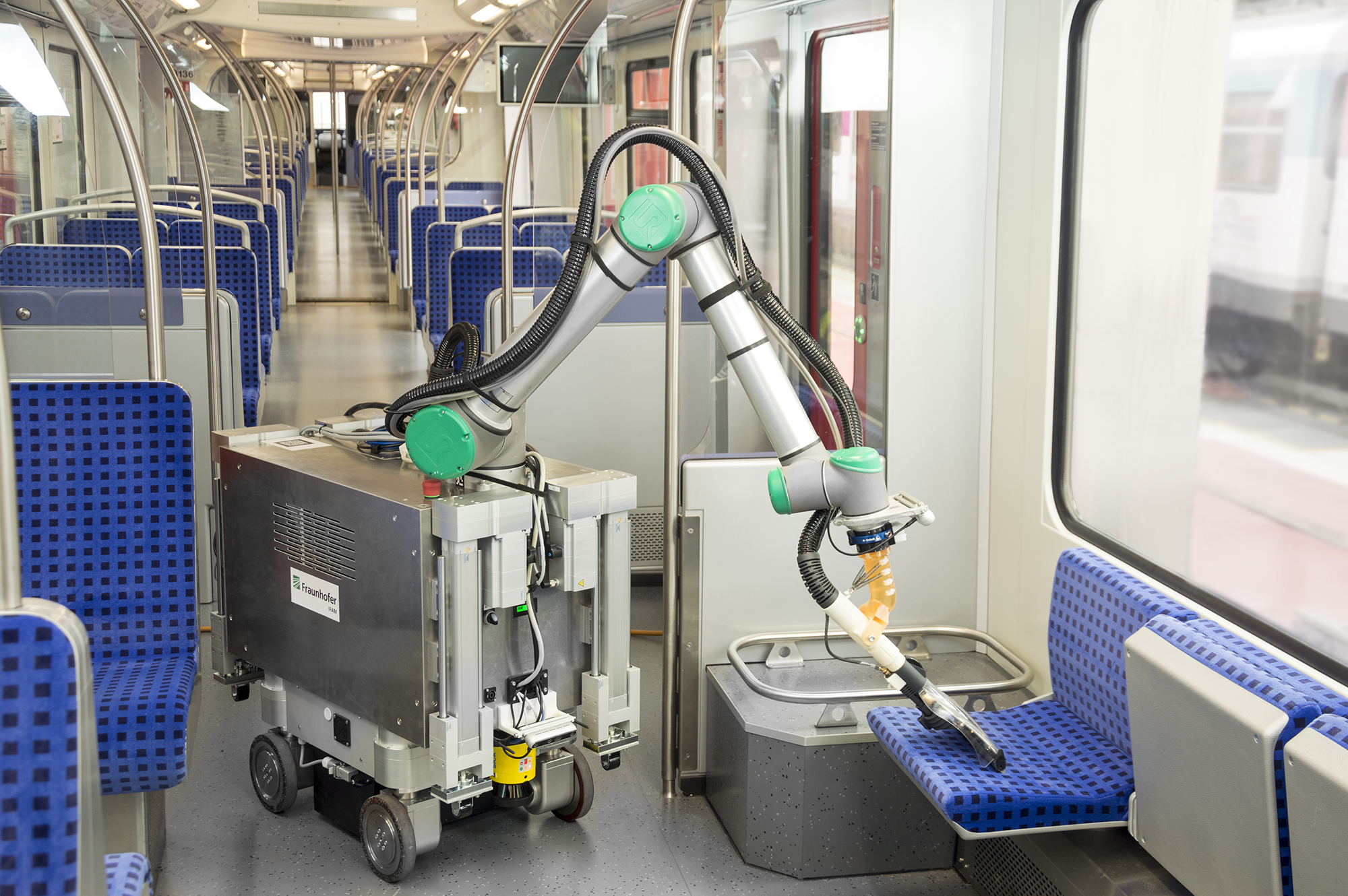
Applied research at InnoTrans 2022 in Berlin, Germany: As part of the “Fraunhofer vs. Corona” program, the automation and production technology experts at Fraunhofer IFAM in Stade, together with project partners, developed a prototype mobile robot platform which uses a lightweight robot and steam cleaner to clean and disinfect surfaces of objects in public transport (PT) vehicles with constant quality in an environmentally friendly manner (https://s.fhg.de/FuEMobDiStade; video). The robot, which navigates autonomously in the vehicles, works with hot dry steam. This dissolves soiling and pathogens – such as viruses and bacteria – with considerably reduced water consumption and without chemical cleaning additives. A suction unit integrated into the brush nozzle removes the detached dirt immediately. The lightweight robot, which uses a camera to recognize objects, automatically guides the cleaning nozzle over the surfaces to be cleaned. Rechargeable batteries supply the entire robotics, including the control system, with energy. Upcoming developments are also intended to ensure mobile supply of the steam vacuum cleaner in the future.
The service robot can not only be seen live in action at the Fraunhofer booth (Hall 23 l Booth 240), but also inside the “IdeasTrain” of S-Bahn Hamburg l Deutsche Bahn (outdoor area T11 l 60).
Corona pandemic and shortage of skilled workers as R&D drivers
What contribution can mobile robotics in public transport and buildings make to combat the Corona pandemic? Twelve institutes and facilities of the Fraunhofer-Gesellschaft addressed this question in the research project “Mobile Disinfection” (“MobDi”) as part of the funding program ”Fraunhofer vs. Corona” with the aim of developing robots and cleaning or disinfection tools within a very short time, investigating their effectiveness and considering economic aspects in this context.
The Corona pandemic poses unprecedented challenges for operators of public buildings and means of transport. The focus is on disinfection and cleaning of surfaces. At the same time, there is a lack of personnel in many areas, while enormous time pressure often prevails. It is therefore not only necessary to simplify this work for the specialists and to relieve them partially, but also to increase the frequency of surface treatment.
Mobile cleaning and disinfection robot for public transport
“As part of the “MobDi” project within a very short time, we have developed a mobile lightweight robot for automated cleaning of various surfaces – such as glass and upholstery – in public transport vehicles, a drive support system to overcome gaps and steps, and an associated cleaning tool based on hot dry steam”, explains deputy project manager Marvin Schulz from Fraunhofer IFAM in Stade and highlights: “It is especially worth emphasizing that this hot dry steam can simultaneously disinfect to a certain degree, eliminating up to 99.9 percent of germs”.
Validation of the mobile robot under real conditions in the S-Bahn Hamburg, Germany, proved that this form of modern service robotics can support the cleaning and disinfection of public transportation and thus achieve added value.
The cleaning and disinfection robot in detail
The robot with a total weight of 330 kg essentially consists of a mobile platform (Automated Guided Vehicle; AGV), a construction for peripheral components and a lightweight robot including a specially developed tool for steam cleaning. A camera with additional depth information for object recognition and referencing is located directly on the robot flange. Four electric cylinders attached to the construction with terminating heavy-duty rollers form a drive support that enables the AGV to independently overcome gaps and smaller steps. In addition, an industrial vacuum cleaner is mounted at the rear of the robot as part of the steam cleaning system to suck up loosened contaminants and is connected to the cleaning nozzle via a hose. A cable leads from the rear wall of the system to the external power supply, which was necessary in this feasibility study to operate the steam vacuum cleaner with a maximum power of 3500 W to avoid additional rechargeable battery packs in the setup.
The mobile platform has an omnidirectional drive, which enables the mobile robot to rotate around its own axis and, above all, to travel with any orientation in any conceivable direction in the plane. This increases the flexibility of the overall system, which is an advantage in confined areas – such as in public transport vehicles. The AGV moves at a maximum speed of 0.9 m/s. It has two laser scanners that can be used for 360° obstacle detection as well as for map recording and subsequent localization and path planning. With the help of electric linear cylinders, one side of the mobile platform can be lifted at a time, or the entire robot can be tilted to overcome a small step in two lifting steps. To cope with larger gaps, all four cylinders can be moved into contact with the ground, thus increasing the wheelbase and the maximum gap width that can be traversed. For both maneuvers, it is only necessary to ensure that one drive pair each (front respectively rear) remains in contact with the ground, as the rollers of the cylinders cannot be actively driven.
The structure located above the AGV contains the necessary electrical components and control units as well as the rechargeable batteries for these components and the lightweight robot. In addition, the components of the steam cleaner of the associated project partner beam GmbH, which have been converted for use in an automation solution, are located here.
The base of a commercially available lightweight robot is mounted on the top plate of the structure. The 6-axis robot has a top speed of 1 m/s, 10 kg payload and a maximum range of 1300 mm. All cables and hoses required at the end effector are routed along the robot without considerably restricting the freedom of movement of the joints in the application. A camera with depth sensor is mounted directly on the robot flange. The camera detects the objects to be cleaned and determines their spatial position and orientation relative to the robot. To ensure that the cleaning tool can be replaced quickly, there is a tool changing system – also fixed to the flange. The end effector specially developed by Fraunhofer IFAM – consisting of a steam nozzle with steam outlet, suction as well as a peel-off lip and cleaning brush – is also equipped with a loose part of the changing system. In addition, the end effector has a spring-loaded compensating kinematic system which equalizes unevenness in the direction of impact of the robot flange and compensates for minor tolerances in object detection.
Successful operation under real conditions and preview of the future
“With the mobile service robot, we were able to successfully demonstrate in the validation environment of our associated project partner S-Bahn Hamburg that both window panes and seat benches in a train car can be cleaned fully automatically”, concludes project manager Björn Reichel, adding: “With the current configuration and minimal adjustments, it was calculated that the windows and seats of an entire S-Bahn train could be cleaned without having to refill fresh water or recharge the system's rechargeable batteries.”
In the future, the field of application can be considerably expanded, as the steam cleaning technology can be used for various surface materials. In addition, object detection can be extended to other objects. However, the adaptability of the nozzle to the geometry of the objects is also crucial, possibly combined with the need for further development of the nozzle or a change during the cleaning and disinfection process.
Challenges arose due to the limited working areas and accessibility with the 6-axis kinematics of the robot as well as the overall size of the system, thus the footprint of the overall system is to be reduced in intended follow-up projects and work could be done with 7-axis kinematics.
The power supply for the cleaning device was provided by a cable that was carried along. In the future, however, the supply via rechargeable batteries could be investigated and implemented in order to increase the self-sufficiency of the system.
More information
Find out more – visit us from September 20 to 23 at InnoTrans in Berlin. The service robot can not only be seen live in action at the Fraunhofer booth (Hall 23 l Booth 240), but also inside the “IdeasTrain” of Hamburg S-Bahn l Deutsche Bahn (outdoor area T11 l 60).
Innotrans 2022 - World Innovation Guide
Video: Mobile cleaning and disinfection robot frees rail vehicles from dirt and pathogens
Automation and Production Technology at Fraunhofer IFAM
Flyer of Stade Branch of Fraunhofer IFAM
Photo
© Fraunhofer IFAM, but can be published in reports about this press release.
www.ifam.fraunhofer.de/en/Press_Releases/Downloads.html
Photo and PDF for Download
Last modified: