A new generation of gap fillers for heat dissipation from batteries in e-cars
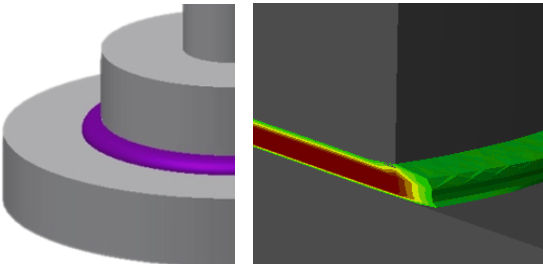
Heat dissipation from batteries is essential to protect them from overheating. This increasingly affects the batteries used in e-cars and other electric vehicles. Only if the batteries are protected from overheating, strong drive performance and long vehicle life can be ensured. This is enabled with TIM (Thermal Interface Materials).
In the field of electromobility, a distinction is made between gap filler materials and TCA (thermally conductive adhesives). Both material classes are based on polymers to which a high proportion of mostly inorganic fillers is added for thermal conduction. The gap fillers are usually soft materials and can only transmit very low mechanical loads. This offers advantages in battery repair and disassembly. TCAs are much stronger after curing of their polymeric portion, and their adhesion to surfaces is high. TCAs will therefore be used as thermally conductive adhesives to provide mechanically durable bonding of series electrical storage components while allowing heat dissipation.
TIM establish a thermal conduction path between the battery module and the cooling system and ensure that the waste heat from the batteries is quickly conducted into the environment. Pasty materials for heat conduction have been used in the past in the smallest quantities in microelectronics, for example to couple electronic components and heat sinks as a thermal paste containing silver. However, much larger quantities of novel gap fillers are needed to cool the batteries used in e-cars, which have to meet new requirements, be processed differently and be designed with significantly less expensive fillers. This results in a high demand for innovation in materials research and manufacturing technology.
Optimization of existing gap filler and TCA concepts
Fraunhofer IFAM was the research partner in the research project OWES (Optimized Heat Dissipation from Energy Storage Systems for Series Electric Vehicles) under the leadership of Audi AG, in which various material science and manufacturing technology solutions for heat dissipation were developed. The focal points of the project included:
- The optimization of existing gapfiller concepts through improved fillers,
- the use of alternative (cheaper, lighter) filler materials,
- new innovative heat dissipation concepts (for example, conductive fabrics)
- the development of testing and simulation methods on the basis of which materials can be assessed with regard to their suitability for use, aging and process, and
- the establishment of processing methods for highly filled pastes required for series production and the development of new, innovative methods such as gap filler injection.
Requirements for a new generation of gap fillers are simultaneously improved thermal conductivity, reduced density and higher economy with suitable mechanical and processing properties. New approaches for optimizing gap fillers were developed and tested in the OWES project, above all through an adapted selection of fillers and suitable matrix polymers.
The project was funded by the German Federal Ministry of Education and Research (BMBF).
Squeeze flow test to measure the compressibility
For processing in series production, the flow properties, i.e. the rheology of the gap filler, must be precisely matched to the production process. Fraunhofer IFAM has developed its own method for predicting the force and counter pressure during the pressing of gap fillers: the so-called squeeze flow test. This is relevant, among other things, for the assembly of the battery cells when they are pressed into the gap filler. When inserting the battery cells into the gap filler-filled battery compartment, there are limits due to the pressure sensitivity of the cells. To ensure that the cells can be pressed in within the available cycle time, the gap filler must exhibit precisely coordinated flow behavior. On the one hand, the pressing forces must not be too high, and on the other hand, the gap filler must have a high yield point.
Coupled fluid structure simulations with high prediction quality were developed and are used by Audi AG for virtual testing of the pressing of gap fillers during the assembly of the battery cells. The entire range of methods developed at Fraunhofer IFAM enables rapid and continuous optimization of materials and processes using sophisticated material science and virtual tools.
Offers for comprehensive characterization of TIM (TCA and gapfiller)
The selection of the right gap filler for the application and manufacturing process is based on the determination of various material properties. The experts at Fraunhofer IFAM will be pleased to support you in selecting possible gap fillers for your individual purpose or in comprehensively qualifying their materials independently. These include thermal conductivity, mechanical properties, aging, processing, curing, and not least disassembly properties. The latter must allow the replacement of individual cells if a battery defect occurs. Fraunhofer IFAM supports you in the characterization and qualification of thermally conductive pastes and is also dedicated to the development of novel gap fillers with improved chemical formulation and optimized manufacturing processes.