Entwicklung neuartiger Schutzbeschichtungen zur Sicherung der Zuverlässigkeit von elektronischen Komponenten
Im ECSEL JU Projekt »Intelligent Reliability 4.0« (iRel40) erarbeiten unter der Leitung der Infineon Technologies AG 75 Partner aus 13 Ländern einen ganzheitlichen Ansatz zur Sicherung der Zuverlässigkeit von elektronischen Komponenten und Systemen (ECS).
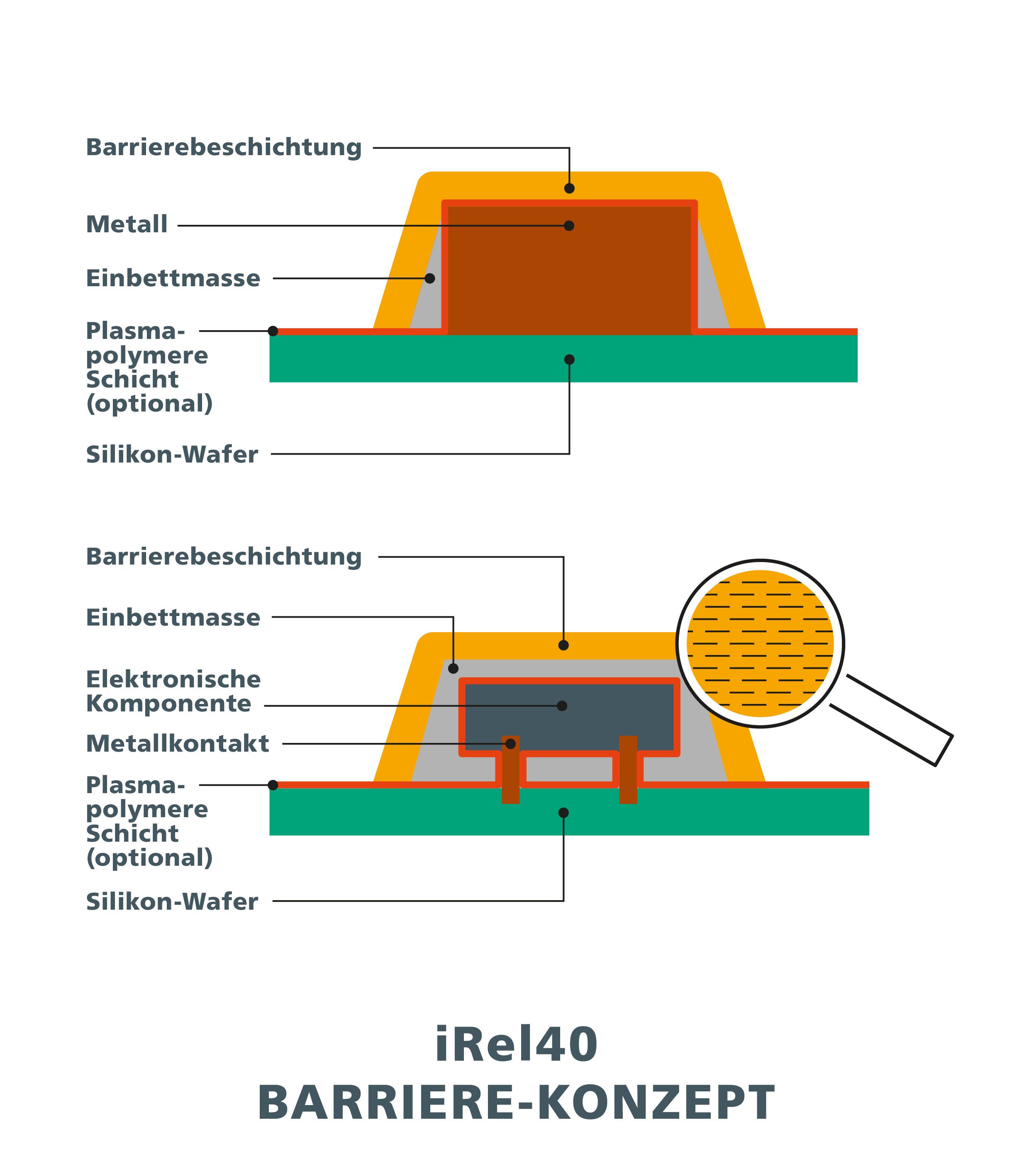
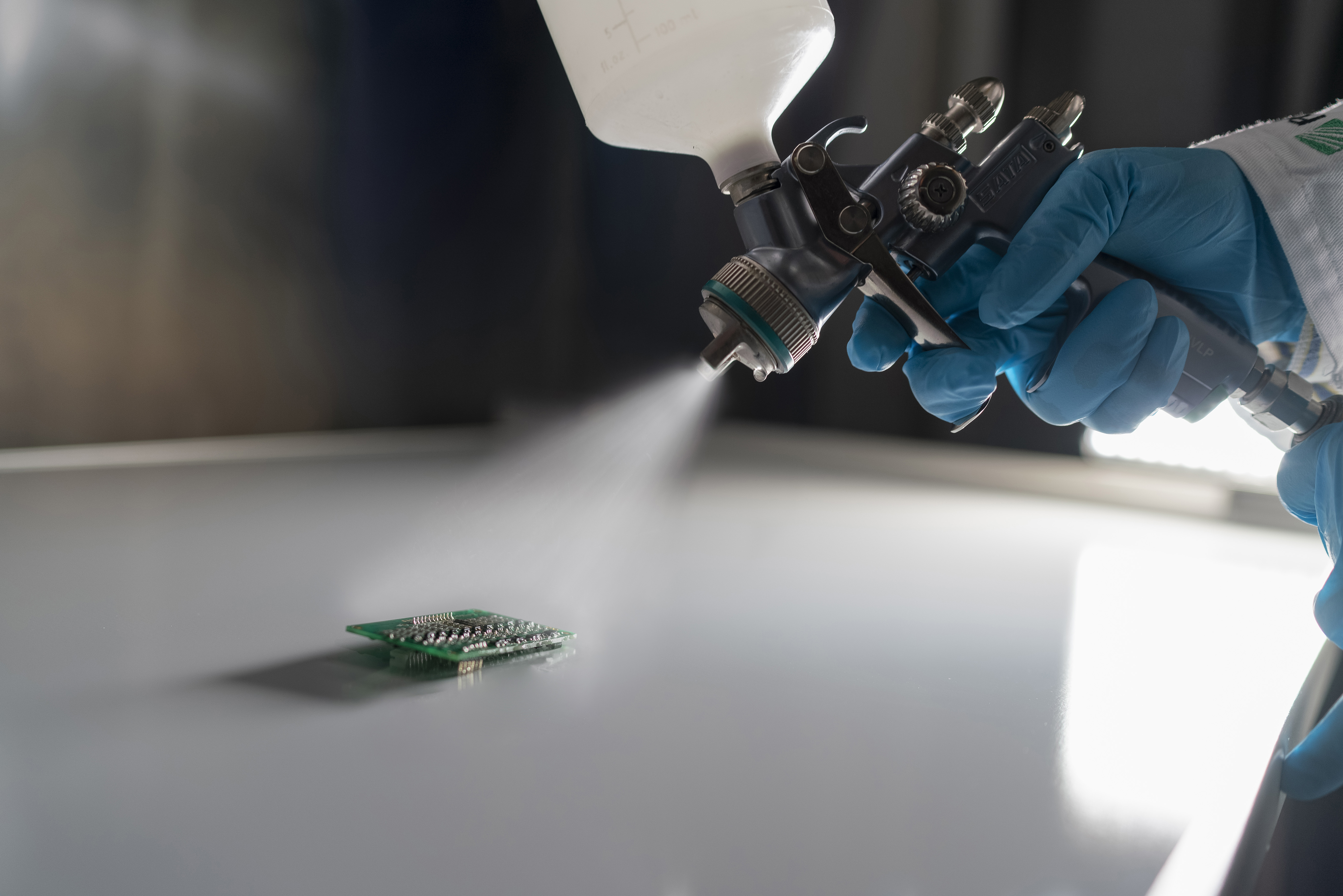
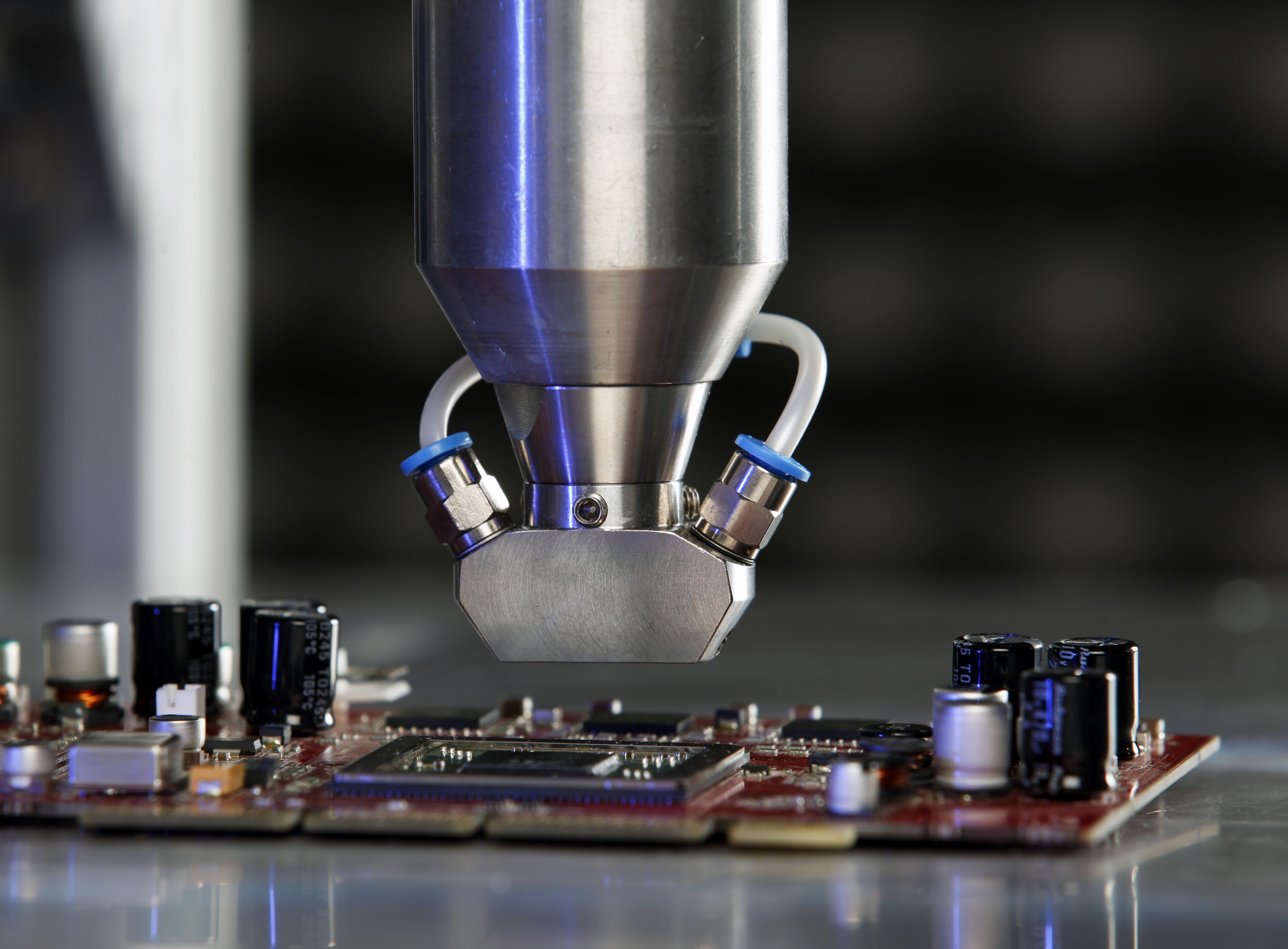
Im Zuge der Miniaturisierung und mit der Entwicklung moderner Produkte sollen immer mehr Funktionen auf engerem Raum integriert werden. Mit diesem Trend steigen gleichzeitig die Ansprüche an elektronische Komponenten und Systeme enorm. Gefordert wird höchste Zuverlässigkeit über den gesamten Lebenszyklus. Dies ist eine elementare Voraussetzung, um neue Technologien bei sicherheitsrelevanten Anwendungen voranzutreiben und zu ermöglichen. Da Korrosionsschäden zu Ausfällen führen können, entwickelt das Fraunhofer IFAM innerhalb des Projektes »Intelligent Reliability 4.0« neuartige Schutzbeschichtungen für mikroelektronische Bauteile zur Sicherung der notwendigen Zuverlässigkeit.
In dem ECSEL JU Projekt »Intelligent Reliability 4.0 – kurz iRel40« kommen unter der Leitung der Infineon Technologies AG erstmals mit 75 Konsortialpartnern die führenden Zuverlässigkeitsexperten und europäischen Hersteller elektronischer Komponenten aus 13 Ländern zusammen, um eine nachhaltige Pan-Europäische Zuverlässigkeits-Community über die nächsten Jahre aufzubauen. Gemeinsam wird das übergeordnete Ziel verfolgt, die Zuverlässigkeit von elektronischen Komponenten und Systemen durch Reduzierung der Fehlerrate entlang der Wertschöpfungskette zu verbessern. »Der Trend zur Systemintegration, insbesondere für heterogene Integration, in der Miniaturisierung, aber auch in der Forderung nach höherer Zuverlässigkeit bei sicherheitsrelevanten Anwendungen wie beispielsweise in der digitalen Industrie, bei der autonomen Mobilität oder etwa in harschen Umgebungen wie bei der Offshore-Energiegewinnung schreiten stetig voran«, erläutert Dr. Volkmar Stenzel, Leiter der Abteilung Lacktechnik und Projektkoordinator iRel40 am Fraunhofer IFAM.
»Wir müssen uns auf diese Herausforderungen vorbereiten, denn die Halbleiterbauelemente und elektronischen Systeme erreichen Grenzen und werden empfindlicher gegenüber den reduzierten Toleranzen immer komplexer werdender Gehäuse- und Board-Technologien. Zudem können sich zahlreiche neue Anwendungen einfach keine Ausfälle leisten. Hierzu sollen durch iRel40 zuverlässige elektronische Komponenten und Systeme schneller entwickelt und neue Prozesse mit höherer Geschwindigkeit in die Produktion überführt werden. Ein tiefes Verständnis durch »Physics of Failure« – also die Physik des Versagens – und Methoden der künstlichen Intelligenz werden Qualität und Zuverlässigkeit vorantreiben. Die Ergebnisse der Entwicklungsarbeiten werden die Produktion entlang der Wertschöpfungskette stärken und nachhaltig den Erfolg von Investitionen in elektronische Komponenten und Systeme in Europa unterstützen«, fasst Volkmar Stenzel den Mehrwert des Projektes zusammen.
Die enge Zusammenarbeit und das Verständnis in Bezug auf die Zuverlässigkeit über die gesamte Wertschöpfungskette hinweg, einschließlich Materialien, Chip, Gehäuse und Board/System, werden herausragendes Wissen generieren, kombinieren und damit die Innovationsfähigkeit verbessern. »Bei den mehr als 30 ausgewählten Industriepiloten nimmt die Materialentwicklung zum Schutz der Komponenten und damit zur Langlebigkeit und funktionalen Sicherheit der Elektronik eine Schlüsselrolle ein. Die dauerhafte Verhinderung von Korrosion ist dabei das Ziel«, betont Stenzel.
Entwicklung zuverlässiger Schutzbeschichtungen zur Vermeidung von Korrosion
Am Fraunhofer-Institut für Fertigungstechnik und Angewandte Materialforschung IFAM entwickeln die Abteilungen Lacktechnik sowie Plasmatechnik und Oberflächen schon lange Technologien zum Schutz von Bauteilen. Eine Besonderheit ist, dass durch das vorhandene Know-how und die Kombination der Kernkompetenzen beider Abteilungen neuartige Schutzbeschichtungen für mikroelektronische Komponenten umfassend bearbeitet werden können. »Die Aufgabe innerhalb des iRel40-Arbeitspaketes „Materialentwicklung und -prüfung für den Bauteilschutz“ besteht in der Entwicklung und Charakterisierung von speziellen Schutzbeschichtungen gegenüber der Diffusion von Wasser bzw. Elektrolytlösungen und Sauerstoff. Durch diese Schichten soll verhindert werden, dass es im Bereich der metallischen Strukturen der mikroelektronischen Komponenten zu Korrosionserscheinungen und dadurch zu Fehlfunktionen oder Bauteilausfällen kommt. Im Fokus der Projektarbeiten stehen insbesondere Mikrochips und Halbleiterstrukturen für Leistungselektronik, die auf Basis von Barriere-Pigmenten und aktiven Korrosionsinhibitoren besser geschützt werden sollen. Weiterhin wird die Kombination dieser Materialien mit plasmapolymeren Schichten untersucht, die für die Aufgabenstellung der Adhäsionsvermittlung unter Wärmebelastung und Schutz vor altersbedingter Unterwanderung gezielt adaptiert werden,« beschreibt Volkmar Stenzel das Entwicklungsvorhaben.
Höherer Schutz durch Kombinationsbeschichtungen
Im Detail besteht das Beschichtungskonzept aus einem neuartigen Mould-Material auf Basis von Silikongelen oder alternativ aus Compression-Mould-Materialien, die hinsichtlich der Anwendung mit aktiven Korrosionsinhibitoren optimiert werden. Zusätzlich wird eine Barriereschicht auf Basis von UV-strukturierbaren Polymeren und speziellen Pigmenten entwickelt. Hierbei kann es sich entweder um zwei einzeln applizierbare Schichten handeln, deren Position im Gesamtschichtaufbau dem Anwendungsprofil angepasst wird, oder aber um eine Kombinationsschicht, in der sowohl der Korrosionsschutz, als auch die Barrierewirkung eingesetzt werden. Hierbei wird neben der Funktionalität vor allem auch ein gutes Entwärmungsverhalten angestrebt.
Zudem werden Plasmapolymerschichten angewandt, die speziell die Fragestellung der Adhäsionsvermittlung zwischen dem metallischen Leiter und Mould-Material bzw. der Schutzbarriereschicht adressieren. Dabei geht es sowohl um den Schutz der Leiteroberfläche bzw. der Bondverbindung für den Fall des Adhäsionsverlustes als auch um den Ausgleich der unterschiedlichen thermischen Ausdehnungskoeffizienten während des Betriebes. Daneben sollen die Schichten die schädlichen chemischen Reaktionen, die im Laufe der Nutzungsdauer entstehen, auf ein Minimum reduzieren.
Insgesamt wird das Schutzsystem Korrosion und andere Schäden durch beispielsweise Feuchtigkeit oder Schadgase verhindern. Dafür wird unter anderem das Mould-Material mit aktiven Korrosionsinhibitoren ausgestattet und bietet somit eine Kombination aus Korrosionsschutz und Vermeidung von Umwelteinflüssen, besonders vor dem Hintergrund der sehr speziellen Anforderungen an Schichtdicke und thermischer Stabilität. Hierfür wird ergänzend eine Barriereschicht entwickelt, die mittels plättchenförmiger Partikel die elektronischen Bauteile gegen Schadgase und Feuchtigkeit abschirmt. Außerdem wird eine Schichtabscheidung durch atmosphärische Plasmatechnik angestrebt, die mit sehr geringen Schichtdicken unter 1 μm die Oberflächen formgenau abschließt und so die Schutzwirkung erhöht, ohne signifikanten Einfluss auf das Entwärmungsverhalten der Bauteile zu nehmen.
Die Kombinationen dieser Technologien werden im Rahmen des Projektes entlang der Wertschöpfungskette in enger Zusammenarbeit mit verschiedenen Partnern aus Forschung und Industrie bewertet und den aktuellen Anforderungen angepasst. Somit wird ein gezieltes und anwendungsorientiertes Vorgehen garantiert und die neuen Technologien können zukunftsweisend optimiert und eingesetzt werden.
Förderung
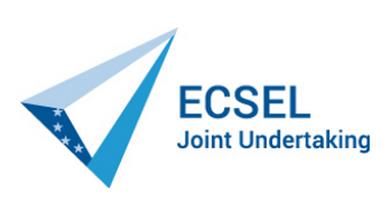
»iRel40« ist ein europäisch kofinanziertes Innovationsprojekt, das vom ECSEL Joint Undertaking (JU) unter der Fördervereinbarung Nr. 876659 bewilligt wurde. Die Finanzierung des Projekts stammt aus dem Forschungsprogramm Horizon 2020 und den teilnehmenden Ländern. Nationale Mittel werden von Deutschland, einschließlich der Freistaaten Sachsen und Thüringen, Österreich, Belgien, Finnland, Frankreich, Italien, den Niederlanden, der Slowakei, Spanien, Schweden und der Türkei bereitgestellt.
Weitere Informationen zum Projekt
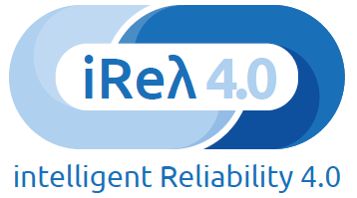
Pressemitteilung und Bilder zum Download
Letzte Änderung: