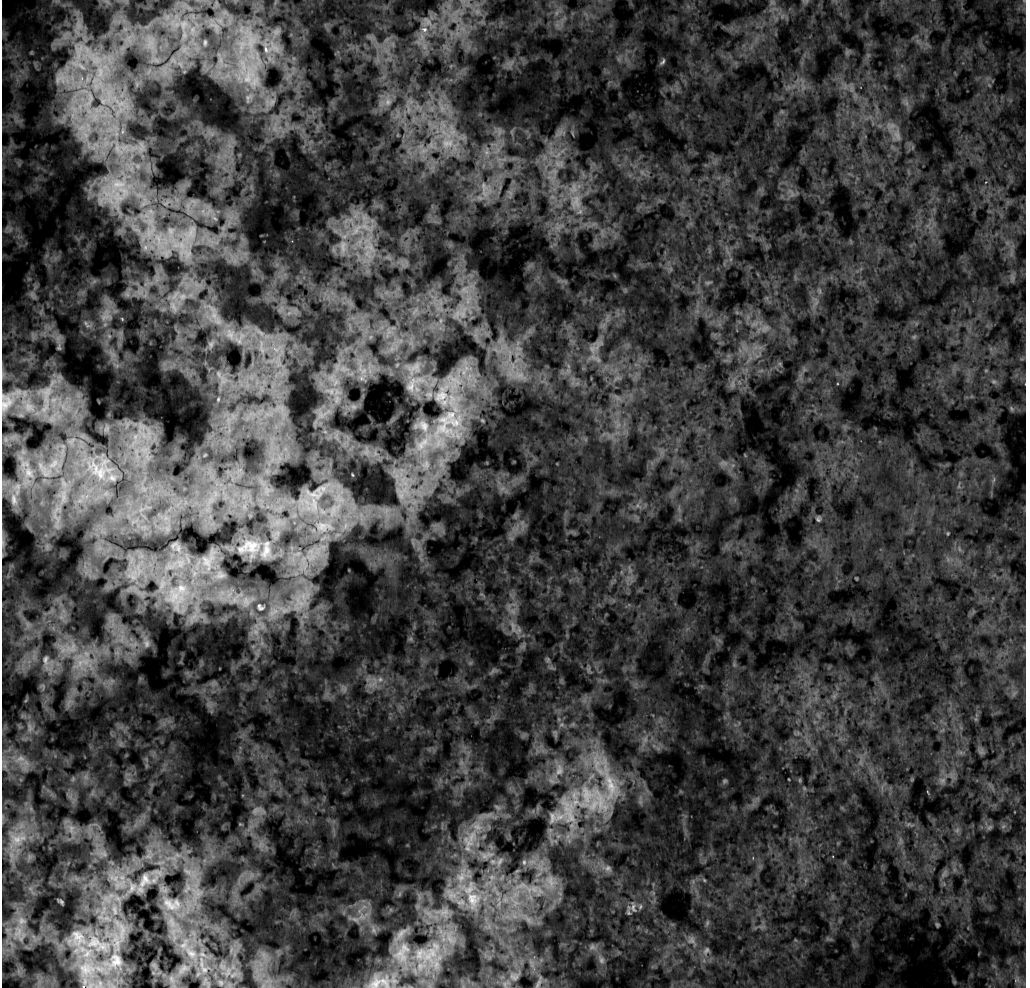
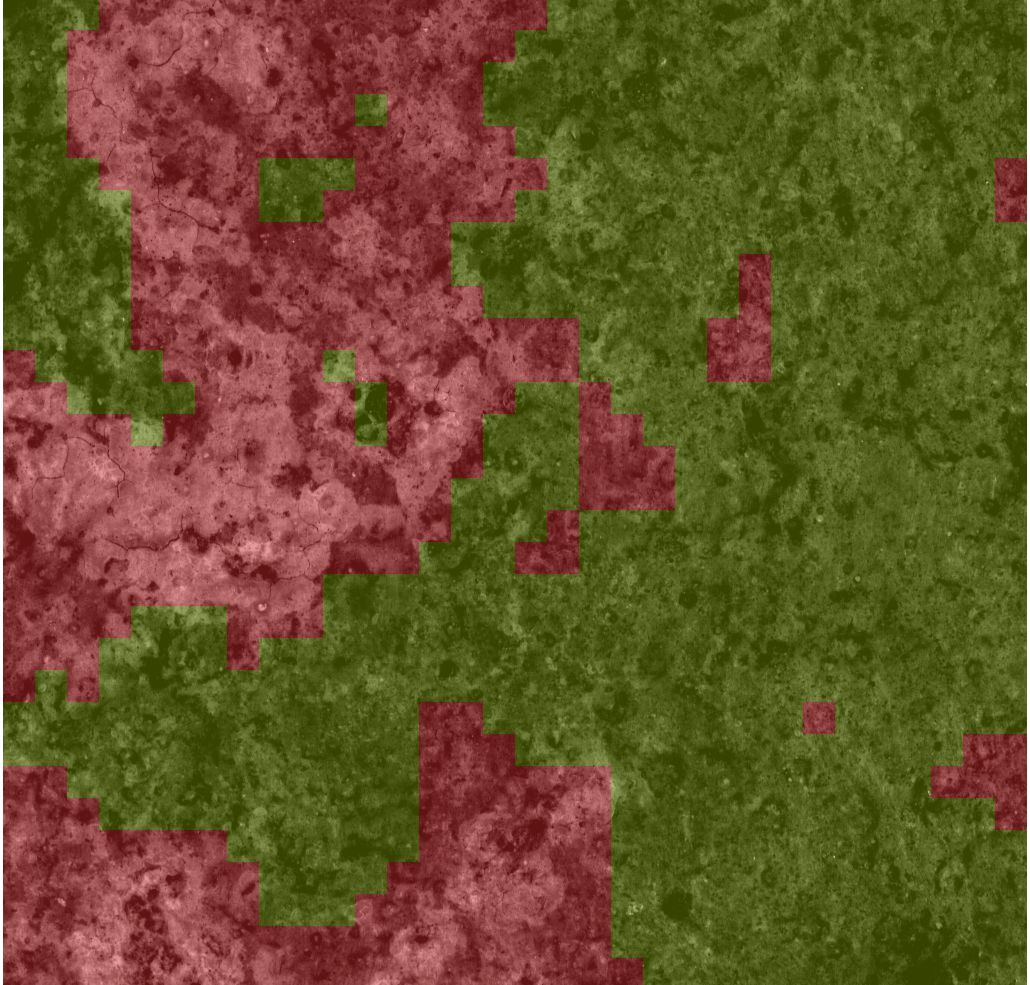
Manuelle Prüfprozesse zur Qualitätssicherung stehen oftmals einer ökonomischen Optimierung von Prozessschritten gegenüber. Durch den Einsatz von künstlicher Intelligenz und maschinellem Lernen können diese Hürden überwunden und die Qualität des Endprodukts sowie die Fertigungsgeschwindigkeit signifikant erhöht werden. Zusätzlich ermöglichen wissensbasierte Algorithmen einen gezielten Wissenstransfer zur Unterstützung von Mitarbeitenden sowie neue digitale Geschäftsmodelle.
Die visuelle Prüfung von Oberflächen oder Bauteilen ist ein wichtiger Prozessschritt im Rahmen der Qualitätssicherung und wird von erfahrenen Fachkräften, wie z. B. zertifizierten Inspektorinnen und Inspektoren, durchgeführt. Doch oftmals unterliegt das Prüfergebnis, trotz der Qualifikation der Prüfenden, einem subjektiven Eindruck, ist nicht reproduzierbar und verursacht dadurch unnötige Standzeiten.
KI-basierte Lösungen
Der Einsatz von automatisierten Bildaufnahmesystemen und KI-basierten Algorithmen stellt für dieses Problem eine innovative Lösung dar. Ein in den letzten Jahren vermehrt genutzter Algorithmus in dem Bereich des maschinellen Lernens ist der Random-Forest-Algorithmus. Dieser kann effizient mit wenigen Bildern von einer Expertin oder einem Experten trainiert werden und bildet anhand verschiedener Merkmale dann sogenannte Entscheidungsbäume, mit denen Expertenentscheidungen nachempfunden werden. Diese angelernten Entscheidungsbäume werden in einer Datenbank gespeichert und genutzt, um unbekannte Bilder auszuwerten. Die Auswertung kann dabei mit hoher Geschwindigkeit sogar live im Prozess erfolgen. Zusätzlich auftretende Fehler oder falsch positiv bewertete Bereiche können jederzeit durch einfaches Nachtrainieren ergänzt und angepasst werden. Zudem bietet dieser Algorithmus, gegenüber z. B. neuronalen Netzen, klare Vorteile in den Möglichkeiten der Nachvollziehbarkeit der Auswertung.
Automatisierte Bewertung für den maritimen Stahlbau
Das Fraunhofer IFAM erforscht und entwickelt entsprechende Algorithmen für die Kleb- und Oberflächentechnik und stellt diese als innovative Produkte seinen Kunden bereit. Durch die maßgeschneiderten Lösungen können Fertigungsprozesse ökonomisch optimiert und die Fertigungsgeschwindigkeit sowie die Qualität des Endprodukts signifikant erhöht werden. In dem aktuellen Projekt »WindsurfAce« wird diese Art der Datenauswertung im maritimen Stahlbau zur Oberflächenbewertung vor dem Auftragen von Korrosionsschutzbeschichtungen angewendet. Die hohen Qualitätsanforderungen, wie beispielsweise für Gründungen von Offshore-Windenergieanlagen, können so sichergestellt werden.Die Expertinnen und Experten des Fraunhofer IFAM in Stade zeigten bereits in vielen Projekten, dass sich durch Erweiterung der Messtechnik, Optimierungen der Software und Anpassungen an der Mechanik die Genauigkeit von Knickarmrobotern erheblich steigern lässt. Sie wiesen an Original-CFK-Flugzeuggroßbauteilen mit Toleranzen im Submillimeterbereich eine hinreichende Präzision bei der Umrissbearbeitung nach. Um den Anwendungsbereich auf Metallbearbeitungsverfahren auszudehnen, sind weitere, auch strukturelle Anpassungen an der Roboterkinematik nötig.
Einen innovativen Ansatz zur Optimierung eines Robotersystems für Bearbeitungsprozesse verfolgt das Projekt »Flexmatik 4.1« (Fraunhofer-internes Programm konzipiert als marktorientierte strategische Vorlaufforschung gemeinsam mit dem Fraunhofer IPK und LBF). Während bisherige Projekte sehr gute Ergebnisse bei kontinuierlichen Fräseingriffen erzielten, ist das Eintauchen in das Werkstück und die flächige Bearbeitung, wenn überhaupt, nur durch aufwendige und prozessverlangsamende Anpassungen möglich gewesen. Der in »Flexmatik 4.1« selbstkonstruierte Roboter mit optimierter Struktur und neu entwickelten Antriebssystemen überwindet diese Einschränkungen und erreicht eine weitere Steigerung der Positionsund Bahngenauigkeit. Durch symmetrischen Aufbau der Kinematik, doppelte Lagerung der Gelenke und zusätzliche Versteifung der Armelemente sind neue, bislang für IR unzugängliche Bearbeitungsapplikationen denkbar.
Eine weitere Schwachstelle bisheriger IR ist die geringe Steifigkeit der Getriebe im Antriebsstrang. Ein zusätzlicher Direktantrieb in der neu entwickelten Kinematik eliminiert deren Einfluss auf die Bahngenauigkeit und erhöht gleichzeitig die Reaktionsgeschwindigkeit bzw. -dynamik. Erste Untersuchungen der Antriebe zeigen eine Steigerung der relativen Bahngenauigkeit im Vergleich zu herkömmlichen Antrieben um den Faktor 10. So lassen sich im Gesamtprozess erheblich höhere Toleranzanforderungen erfüllen.
Mit der Einführung der Robotik in die Großbauteilbearbeitung ist eine erhebliche Kostensenkung bei gleichzeitiger Effizienzsteigerung möglich. Dies ist ein weiterer Beitrag, um die Nachhaltigkeit in der Produktion zu verbessern und den deutschen zivilen Flugzeugbau im internationalen Wettbewerb zu stärken.