Batterieherstellung mittels 2D- und 3D-Druckverfahren
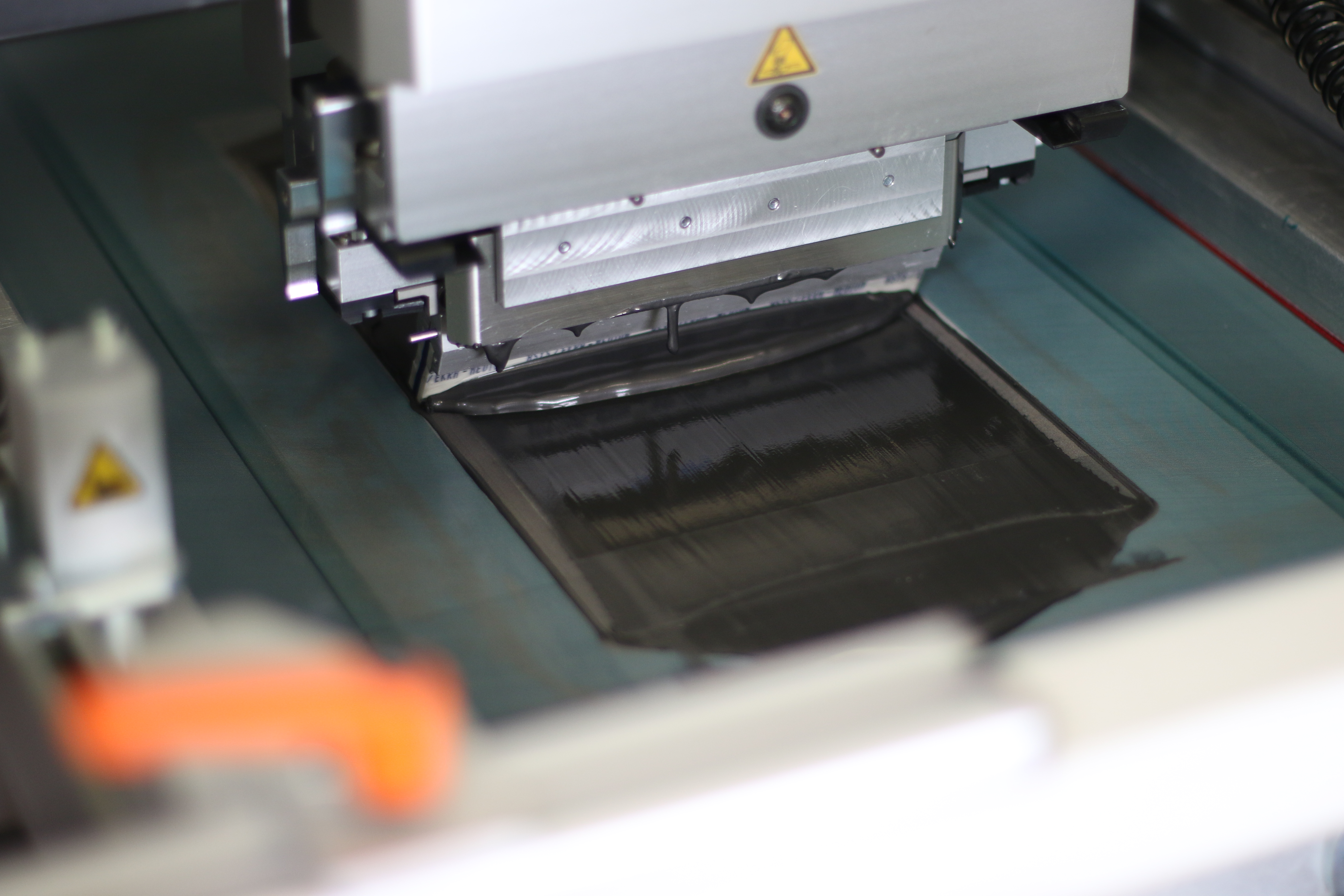
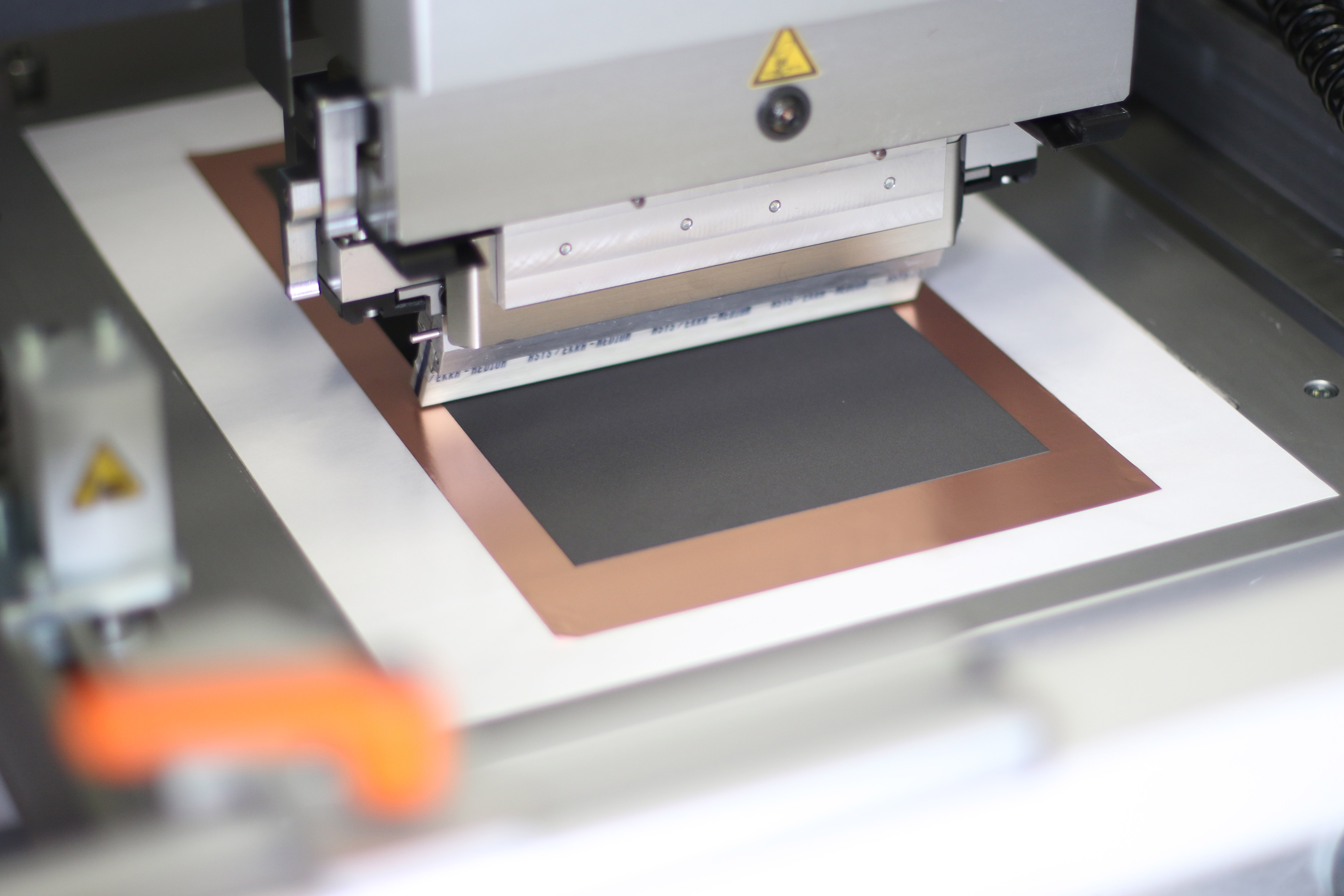
Fertigungstechnologie für Batterien der Zukunft: Mithilfe des Siebdruck-Verfahrens bietet das Fraunhofer IFAM Alternativen für die Batteriefertigung. Neue Fertigungskonzepte ermöglichen dabei höhere Aktivmaterialbeladungen sowie größere Freiheiten im Elektrodendesign. Komplett gedruckte Batterien verhelfen einerseits dazu, sich von den Einschränkungen der aktuellen Fertigungstechnik zu lösen und andererseits den Einsatz von Lösemitteln und nachfolgender Trocknungsprozessen zu reduzieren. Das Fraunhofer IFAM verbindet dabei Batterie-Expertise mit fundiertem Know-how in der Additiven Fertigung.
Nachhaltige Batterie der Zukunft
Das Thema Energiespeicher ist aktuell so präsent wie nie zuvor. Die größten Herausforderungen sind dabei unter anderem die Erhöhung der spezifischen Energiedichte oder eine verbesserte Umweltfreundlichkeit durch die Nutzung alternativer Materialien und eines verbesserten Recyclings. Um diese Herausforderungen zu meistern, erforscht und entwickelt das Fraunhofer IFAM umweltfreundliche Energiespeichertechnologien und Prozesse, sowie Festkörperbatterien, welche durch neue Fertigungstechniken wie z.B. dem Mehrfachdruck mittels Siebdruck hergestellt werden. Dabei konnten bereits Prototypen von additiv gefertigten Batterien entwickelt werden.
Über die Herstellroute lassen sich am Fraunhofer IFAM im Vergleich zur konventionellen Elektrodenherstellung dickere Elektrodenschichten herstellen, wodurch höhere Energiedichten realisiert werden können. Des Weiteren werden durch den endformnahen Druck neue Elektrodendesigns ermöglicht und höherer Realbeladungen mit verringertem Lösungsmitteleinsatz erreicht. Der Fertigungsprozess eignet sich dadurch nicht nur für den Prototypenbau, sondern ermöglicht eine anwendungsspezifische »Batterieherstellung-on-Demand«.
Ein weiterer wichtiger Forschungsschwerpunkt des Fraunhofer IFAM liegt in der Entwicklung neuer Druckpasten auf Basis umweltfreundlicherer Nickel- oder Kobalt-freier Materialien sowie wasserbasierter Rezepturen.
Additive Fertigungsverfahren für die Batteriefertigung
Unsere Expertinnen und Experten besitzen umfassendes Know-How in der Pastenherstellung für gedruckte Elektroden. Dieses umfasst die Auswahl geeigneter Materialien (Aktivmaterialien, Leitadditive, Binder, Rheologie-Additive, Lösemittel), die Formulierung der Paste entsprechend den individuellen, spezifischen Anforderungen des Anwendungsfalles der zu erstellenden Batteriezellen und der Homogenisierung der Pasten mittels geeigneter Dispergierverfahren (z.B. Dispermat, Dreiwalzwerk oder Extruder).
Der Siebdruckprozess stellt eine Möglichkeit der Herstellung von dicken Elektrodenschichten dar. Je nach zu erstellendem Elektrodentyp mit entsprechendem Elektrodenmaterial und Ableitersubstrat werden am Fraunhofer IFAM die Druckprozessparameter optimiert. Diese umfassen unter anderem das Siebdesign, die Gewebeart, der genutzte Rakelwinkel/-druck, der Druckmodus oder die Druckgeschwindigkeiten.