Fertigung von FVK-Bauteilen durch funktionalisierte Trennfolie PeelPLAS®
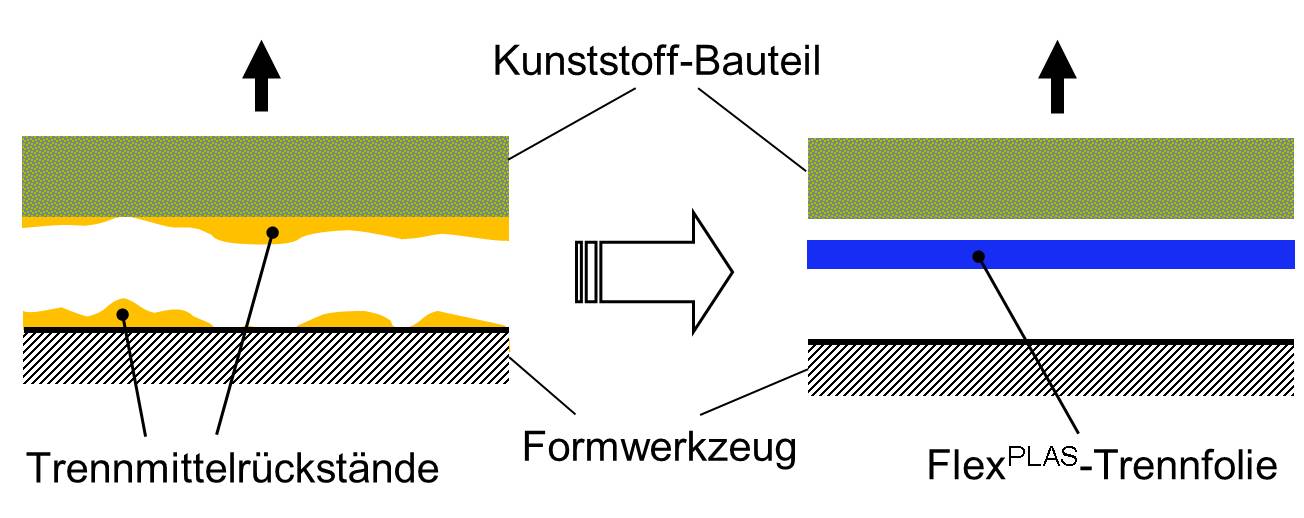
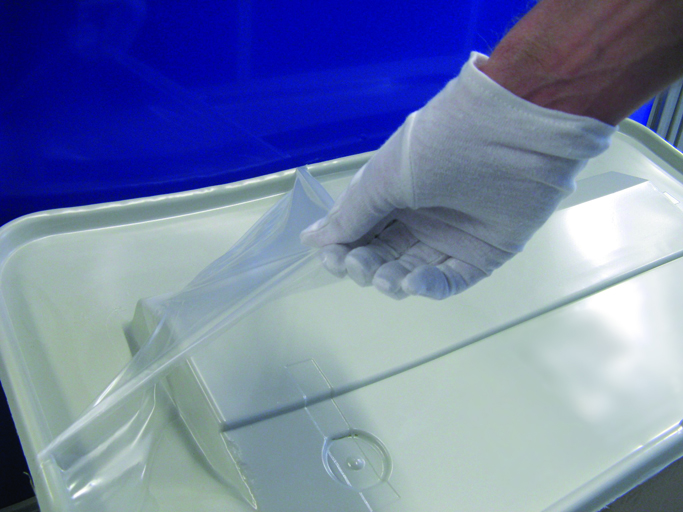
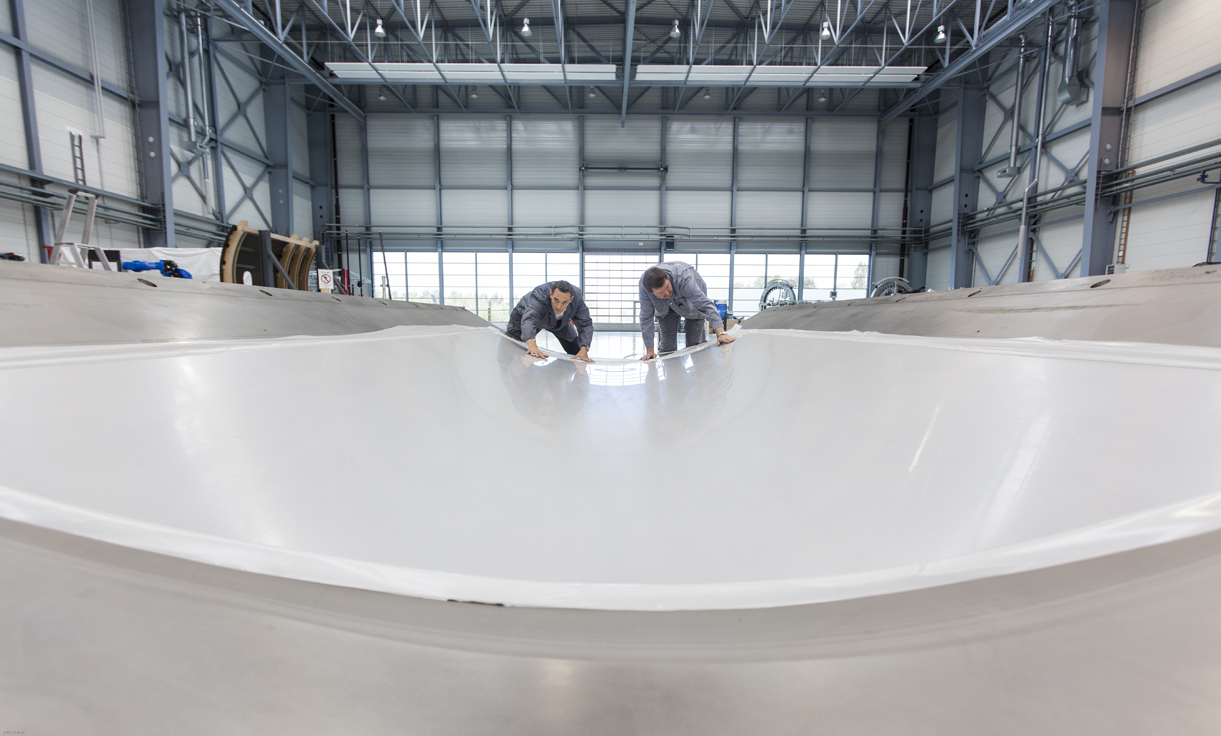
Bauteile aus Faserverbundkunststoffen (FVK) sind durch ihr geringes Gewicht und ihre Festigkeit in den unterschiedlichsten Branchen wie der Luftfahrt- oder der Automobilindustrie besonders gefragt. Die konventionelle Entformung von FVK-Bauteilen durch den Einsatz von Trennmitteln ist allerdings sehr kosten- und arbeitsintensiv. Zudem können die Trennmittel schädliche Einflüsse auf die Umwelt haben. Am Fraunhofer IFAM wurde eine plasmabeschichtete Trennfolie entwickelt, mit der duroplastische Kunststoffbauteile ohne die Verwendung von Trennmitteln gefertigt und sicher entformt werden können. Die Bauteiloberfläche ist frei von Kontaminationen und kann direkt lackiert oder verklebt werden.
Produktion ohne Trennmittel: Die PeelPLAS®-Trennfolie senkt Materialkosten, steigert die Produktivität und schützt die Umwelt
Häufig werden herkömmliche Trennmittel genutzt, um Bauteile nach der Fertigung sicher aus der Form zu lösen. Die dabei verbliebenen Trennmittelreste müssen anschließend sowohl auf dem Bauteil als auch auf dem Werkzeug durch Abschleifen oder Strahlen entfernt werden. Ein zeit- und kostenintensiver Prozess, der zudem die Umwelt belastet und die Gesundheit der Mitarbeiter durch erhebliche Lärm- und Staubemissionen gefährdet.
Mit der PeelPLAS®-Trennfolie hat das Fraunhofer IFAM einen Ersatz für den Einsatz von Trennmitteln bei der Entformung von Kunststoffbauteilen entwickelt. Die Polymerfolie ist mit einer extradünnen plasmapolymeren Trennschicht versehen. Das Besondere an dieser ReleasePLAS®-Beschichtung: Sie haftet optimal auf der Polymerfolie, zeigt gegenüber den meisten Reaktivharzen jedoch eine sehr gute Trennwirkung. Die hochelastische Folie hält Dehnungen bis zu 300 Prozent und Aushärtetemperaturen bis zu 190°C stand und lässt sich so problemlos auch auf gekrümmte und strukturierte Formen aufbringen. Sie wird wie eine zweite Haut auf die Formoberfläche gezogen und kann nach der Aushärtung der duroplastischen Matrix rückstandsfrei von der Bauteiloberfläche entfernt werden. Es wird eine saubere Bauteiloberfläche freigelegt, die direkt weiterverarbeitet werden kann. Wird die Folie zunächst auf dem Bauteil belassen, kann sie außerdem als Transportschutz dienen sowie das Bauteil bei der Weiterbearbeitung wie dem Besäumen oder Bohren vor Verunreinigungen schützen.
Je nach Anforderungen werden unterschiedliche Polymerfolien verwendet. Die flexiblen Trennfolien sind für die meisten Reaktivharze wie beispielsweise Epoxid-, Vinylester-, Cyanatester- und Phenolharze geeignet. Ein weiterer Pluspunkt: Auch die Verwendung von In-Mould-Coatings für eine Lackierung in der Form ist möglich, beispielsweise mit Polyurethan-Gelcoats. Der Lack wird dabei in einem Produktionsschritt mit dem Bauteil ausgehärtet.
Prepreg, Resin Transfer Moulding, Pressverfahren – verschiedenste Fertigungsverfahren sind möglich
Ursprünglich wurde die PeelPLAS®-Trennfolie für die Fertigung von Großstrukturen aus Faserverbundkunststoffen (FVK) – wie sie beispielsweise beim Bau von Flugzeugen oder Windenergieanlagen verwendet werden – entwickelt. Inzwischen haben die Forscherinnen und Forscher des Fraunhofer IFAM sie für viele zusätzliche Fertigungsverfahren weiterentwickelt. Dazu gehören neben dem (Vakuum-)Infusionsverfahren und der Prepreg-Technologie, auch das Resin Transfer Moulding (RTM) sowie Pressverfahren. Die Trennfolie wird durch Evakuieren wie eine zweite Haut auf die Form streckgezogen und kann somit ohne Probleme auch in komplexen Geometrien eingesetzt werden. Dies ist in der Regel schon bei Raumtemperatur möglich. Die dafür nötige Abdichtung am Werkzeugrand, sowie der benötigte Vakuumanschluss können meist mit einfachen Mitteln auf bestehenden Werkzeugen umgesetzt werden. Die innovative Entformungstechnik ist daher besonders kostengünstig umsetzbar. Wird der Einsatz der Trennfolie bereits bei der Anlagenplanung und Werkzeugkonstruktion berücksichtigt, erhöht sich die Wirtschaftlichkeit noch weiter.
Dr. Matthias Ott ist stellvertretender Leiter der Abteilung »Plasmatechnik und Oberflächen« am Fraunhofer IFAM. Das Institut beschäftigt sich seit vielen Jahren mit der Entwicklung von umweltfreundlichen Trennmittelersätzen. In der Abteilung »Plasmatechnik und Oberflächen« liegt der Fokus dabei auf der Beschichtungstechnik. Die plasmapolymeren Trennschichten kommen u.a. in der Automobilindustrie zum Einsatz. Mit der PeelPLAS®-Trennfolie kann nun auch die Fertigung von Faserverbund-Großstrukturen realisiert werden.