Analytics of Heat Treatment
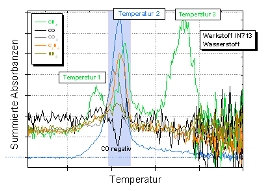
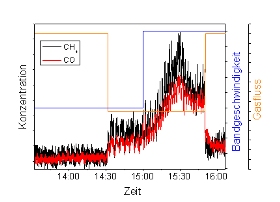
The goal of process analytics is the efficient optimization of the heat treatment process. Through a deeper understanding of the thermochemical processes during debinding and sintering, we can improve component quality and make process control more economical. Originally developed to optimize the production of cellular metals with high organic contents, the principle has now been applied to the further development of metal powder injection moulding and to classical powder metallurgical production.
Access to these processes is provided by the process gas composition, which can be measured directly in the furnace at the Fraunhofer IFAM Dresden. The method provides temperature-accurate information about the beginning and end of decomposition or reduction processes. Thus heat treatment processes such as debinding, reduction and sintering processes can be reliably characterized and efficiently designed or optimized. Such measurements can be carried out both in our laboratory furnaces and on production plants on site.